By: Ed Fontes, CTO, COMSOL, Inc.
The biggest challenges for battery design are energy density, power density, charging time, life, cost, and sustainability. Modeling and simulation are very efficient methods that can assist researchers, developers, and designers in meeting these challenges.
Energy density is limited by the battery’s chemistry, which even without losses limits the theoretical energy density. The chemistry is defined by the electrode material and the composition of the electrolyte.
Lithium-air batteries get close to the energy density of gasoline, which is probably close to the maximum energy density for a battery.
However, the components required for thermal management and current collection contribute to the total weight of the battery system. The design of these components can substantially influence the energy density of a battery system.
Power Density and Fast Recharge
The power density of a battery is important for the efficiency of electric vehicles. A high power density is required to recapture high amounts of energy in a short time during regenerative braking or fast recharge.
This gives a difficult optimization problem, since the system has to cope with very high current densities during recharge and relatively low current densities during discharge.
It also relates to the design of the thermal management and the current collectors mentioned earlier. In addition, the design of fundamental battery components such as the electrodes, separator, and electrolyte are of great importance for power density.
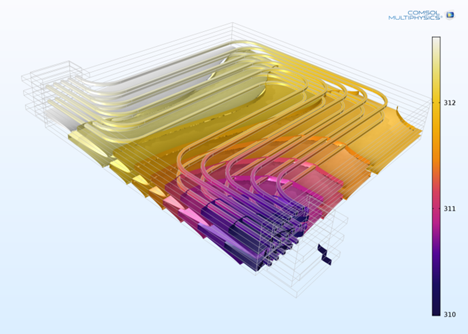
Life, Reliability, and Safety
Life is a major consideration where safety and reliability are closely related. Discharge, wear, and failure should occur slowly and in a controlled and transparent way.
This is not only an issue of the chemistry of the battery, but also of the design, since uneven current density distribution and poor control of discharge/recharge and of the thermal management system may accelerate wear and increase the risks of failure.
Short-circuits formed by metal deposition may be responsible for decrease in performance as well as an increased risk for runaway heating. Technologies for state-of-health monitoring are required in order to continuously assess the state of the battery system and the risks of failure.
Costs
The manufacturing process for high-power batteries and electric powertrains is not as optimized as for mechanical powertrains for combustion engines. There is a larger potential in productivity gains and decreased costs by large-scale production in the manufacturing process for the battery components.
Sustainability
The development of new batteries has to include the aspect of sustainability. There has to be a strategy for mining, recycling, producing, and disposing of new battery types. This is primarily a legal matter for governments, but also a commercial consideration for battery manufacturers and automotive companies.
Figure 2. The goal with this application is to explain experimental electrochemical impedance spectroscopy (EIS) measurements and to show how you can use the model and the measurements to estimate the properties of lithium-ion batteries. The application takes experimental data from EIS measurements as input, simulates these measurements, and then runs a parameter estimation based on the experimental data
Modeling and Simulation
The understanding and optimization of fundamental components of the battery; such as electrodes, electrolyte, and separator; can be accelerated using modeling and simulations. The systems for thermal management, current collection, and state-of-health monitoring can also be developed with high-fidelity multiphysics simulations.
Figure 1 shows a model for the optimization of the channels in the cooling plates of a battery pack. The is a common application in the automotive industry. For example, Fiat Research Center uses mathematical modeling for studying thermal management of pouch cells for hybrid vehicles1.
Fundamental studies of battery components as well as the development of state of health methods can be very efficiently carried out by combining experimental measurements of electrochemical impedance spectroscopy (EIS) with mathematical models, see the article from the French research institute CEA2.
Figure 2 shows an app, where experimental data can be imported and used in a physics-based model of EIS. This allows for the estimation of parameters such as activity of the electrodes, surface area, electrical conductivities of the different components, mass transport properties of reactants and products, and state of charge of the electrodes.
References