As India races to become a global manufacturing powerhouse, a quiet revolution is reshaping factory floors across the nation. From EV batteries to electronics, manufacturers are discovering that yesterday’s waste streams can become tomorrow’s profit centres – exemplifying the concept of circular economy, where sustainability meets business success.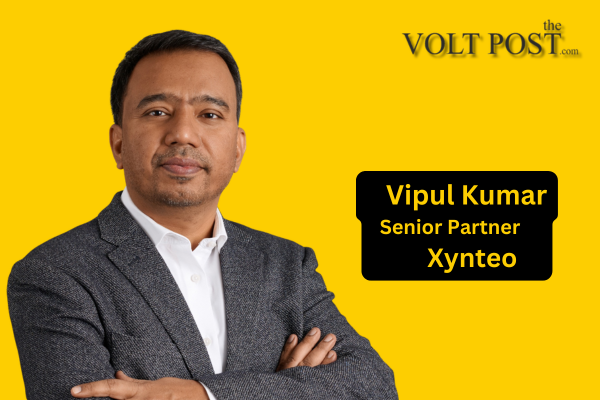
In an era where resource scarcity and climate change pose unprecedented challenges to industrial growth, the manufacturing sector stands at a crossroads.
The traditional linear “take-make-dispose” model is no longer sustainable – environmentally or economically. As India positions itself as a global manufacturing hub, the imperative to embrace circular economy principles has never been stronger. This transformation isn’t just about environmental responsibility; it’s about reimagining how we create and capture value in manufacturing.
The mounting challenge of manufacturing waste
The manufacturing sector in India generates significant industrial waste, with a large portion still ending up in landfills rather than being recycled or reused. This isn’t just an environmental crisis – it represents billions in lost economic value. From heavy industries to electronics manufacturing, valuable materials that could be recaptured and reused are instead being lost to waste.
In fact, the environmental impact extends beyond waste. The linear manufacturing model contributes significantly to greenhouse gas emissions, water pollution, and resource depletion.
As regulations tighten and consumers become more environmentally conscious, manufacturers who cling to traditional models risk both their reputation and their bottom line
Reimagining manufacturing through circular principles
The circular economy represents a fundamental shift in how we approach manufacturing. Instead of the traditional extract-use-dispose model, circular manufacturing creates closed loops where materials and products are kept in use for as long as possible. This isn’t just about end-of-life recycling – it’s about rethinking the entire manufacturing process from design to disposal.
Xynteo’s work in India’s electric vehicle battery sector provides a compelling example of circular economy principles in action. NITI Aayog projects that by 2030, India will have 128 gigawatt-hours of recyclable batteries available, with EVs accounting for 46% of this volume. The market opportunity is significant – global estimates suggest the battery recycling market could expand to over USD 95 billion annually by 2040. However, India’s current recycling capacity stands at just 2 gigawatt-hours, highlighting the urgent need for infrastructure development.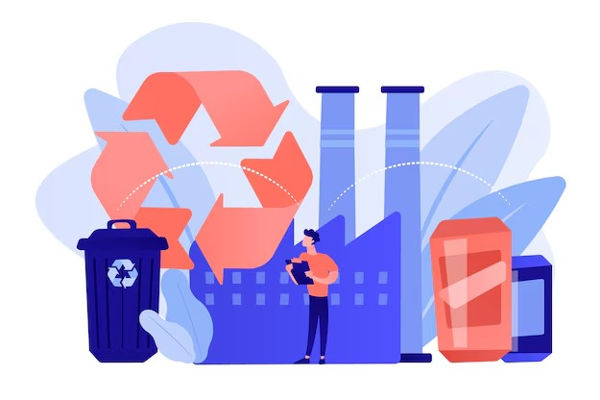
The battery sector exemplifies both the challenges and opportunities in transitioning to circular manufacturing. Currently, most of India’s recyclers produce only black mass, which is typically exported for further processing. This represents a missed opportunity for domestic value creation.
Furthermore, the absence of proper reverse logistics processes and standardised labelling systems complicates efficient collection and sorting. Yet these challenges are driving innovation across the value chain.
Manufacturers are developing new technologies for battery health diagnostics, exploring second-life applications, and creating innovative business models around battery reuse and recycling.
Technology as an enabler of circularity
Digital transformation is accelerating the shift to circular manufacturing. Advanced analytics and Internet of Things (IoT) sensors are helping manufacturers optimise resource use and minimise waste in real-time.
Artificial Intelligence is enabling predictive maintenance systems that extend equipment life and reduce material waste.
These technologies aren’t just improving efficiency – they’re enabling entirely new business models based on product-as-a-service and shared resource utilisation.
The economic case for circular manufacturing
The business benefits of circular manufacturing extend far beyond waste reduction affirms Vipul Kumar – Senior Partner, Xynteo. Companies implementing circular principles are seeing significant savings in raw material costs while discovering new revenue streams from recovered materials and refurbished products.
In the battery sector, for instance, recycling and reuse strategies are becoming increasingly crucial for addressing raw material security. While India has discovered 5.9 million tonnes of lithium reserves, developing these mines will take 8-10 years. Circular economy principles offer a way to bridge this gap while creating new value streams.
Vipul Kumar – Senior Partner, Xynteo states that the economic opportunity extends across sectors. In the automotive sector, remanufactured parts represent an emerging opportunity for value creation.
Electronics manufacturers are finding value in take-back programs and modular design principles. These initiatives don’t just reduce costs – they create new revenue streams and strengthen supply chain resilience.
Overcoming the implementation challenge
The transition to circular manufacturing requires addressing multiple challenges simultaneously.
Take the battery sector: producers often express scepticism about the quality of recycled materials, highlighting the need for stringent quality control and standardisation.
Limited investment in R&D hampers innovation in recycling technologies and second-life applications. These challenges are not unique to batteries – manufacturers across sectors face similar hurdles in implementing circular practices.
Success requires a systemic approach. Companies need to look beyond their own operations and engage with suppliers, customers, and even competitors to create effective circular systems.
Industry coalitions are proving particularly effective in addressing shared challenges. For example, leading battery manufacturers are collaborating on collection infrastructure and recycling technologies, sharing both costs and expertise to accelerate the transition to circularity.
Building a circular future
The path to circular manufacturing requires both vision and practical action. Leadership commitment is essential – this isn’t just an operational change but a strategic transformation that affects every aspect of the business.
Companies need to invest in developing circular economy competencies across their workforce and foster a culture of innovation that challenges traditional linear thinking.
Collaboration is key to scaling circular solutions. No company can create a circular economy alone. We’re seeing promising examples of cross-industry collaboration, like the partnership between automotive manufacturers and battery recyclers to create closed-loop supply chains for electric vehicle batteries.
The way forward
As India aims to become a global manufacturing powerhouse, circular economy principles offer a pathway to sustainable growth.
The transformation won’t happen overnight, but manufacturers can take concrete steps today by conducting a thorough assessment of waste streams and material flows; identifying opportunities for immediate waste reduction and material recovery; investing in digital technologies that enable better tracking and optimisation of resources; and most importantly, engaging with industry partners to develop shared solutions to common challenges.