There has been a lot of research on Additive Manufacturing (AM), also known as 3D printing, to manufacture Ti-6Al-4V alloys, using Laser-Based Powder Bed Fusion (LPBF)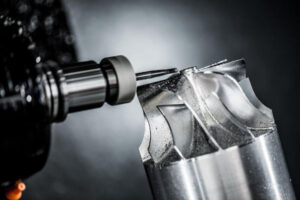
Did you know that the Greek mythological Titans inspired the naming of titanium? The Titans were supposedly the twelve offspring of Gaia (Earth) and Uranus (Sky). There were six male and six female children. The history and drama surrounding the Titans is extensive. It resembles a Greek version of “Game of Thrones.”
But in reality, titanium is actually a very useful element, which exists in its natural state as an oxide. Titanium alloys, in particular, are strong, lightweight, and versatile, finding applications in aerospace, automotive, military, and bioimplant industries.
Ti-6Al-4V, or (titanium-aluminum-vanadium), alloy is one of the most widely used types of titanium alloy and is used in a variety of industries, including the energy, automotive, maritime, and chemical sectors. This is because to the advantageous qualities of Ti-6Al-4V, which include great corrosion resistance, high strength, low density, high fracture toughness, and biocompatibility.
It’s nice to know that Ti-6Al-4V is used to make the Boeing 787 and Airbus A350 aircrafts, and is also used to make high-performance race cars.
It is, consequently, understandable that we should know more about the properties of such a valuable alloy. In recent years, there has been a lot of research on Additive Manufacturing (AM), also known as 3D printing, to manufacture Ti-6Al-4V alloys, using Laser-Based Powder Bed Fusion (LPBF). This method has been useful in making near-net-shaped products with complex geometries at industrial scales.
The rapid heating and cooling in this manufacturing process leads to the formation of non-equilibrium and metastable phases. One of the metastable phases called the ?’-martensite phase (alpha-dash-martensite), formed during the fabrication of Ti-6Al-4V, and its subsequent decomposition into ?- (alpha-) and ?- (beta-) phases upon suitable heat treatment need to be studied in great detail.
The decomposition of the ?’-martensite phase into ? and ? phases evolves the formation of the ?/? interface. This interface is important as it could act as a barrier to the motion of dislocation and thus plays a significant role in the strengthening of Ti-6Al-4V alloy. It is also a crucial factor in deciding the tensile strength and fracture toughness of the Ti-6Al-4V alloy. There are not many studies that concentrate on the path of evolution during the decomposition of such metastable phases. Therefore, the novelty of this work is to trace out the pathway of such phase transformations.
It is well known that the chemical composition, phases, and microstructure largely determine the mechanical properties of an alloy. It is therefore, necessary to study at both the atomic level and the bulk level to better understand the evolution of the microstructure and its effect on mechanical property.
The authors of this study, Dr. D. Kesavan from the Department of Mechanical Engineering, Indian Institute of Technology Palakkad, Kanjikode, India, and Ms. S. Usha Rani, Dr. M. Sadhasivam, Dr. K. G. Pradeep, and Prof. M. Kamaraj from the Department of Metallurgical and Materials Engineering, Indian Institute of Technology Madras, Chennai, India, have examined the segregation tendency and partitioning behavior of various elements during phase transformation of Ti-6Al-4V alloy in both as-built (original) and annealed (modified) conditions.
Here the Correlative Microscopic Technique involving Transmission Electron Microscopy (TEM), Transmission Kikuchi Diffraction (TKD), Energy Dispersive X-Ray Spectroscopy (EDS), and Scanning Transmission Electron Microscopy (STEM) were used to study the microstructure, crystallographic information and chemistry respectively at the same region of interest from bulk to nano scale in order to map the phase transformations.
Further, Atomic Probe Tomography (APT) was used to analyze the ? phase evolution at a near-atomic scale resolution The APT is a state-of-art and a powerful technique to visualize the 3D atom maps with a chemical sensitivity down to 10 ppm for all the elements in the periodic table even for Hydrogen!
It was found that low temperature annealing at 750 ?C, the transformation is triggered by segregation of ?-stabilizer i.e. vanadium-rich regions into the ?-phase in the form of nanoscale precipitates. At an annealing temperature above 800?C, the ?-phase transformation gets completed with a lath-type morphology.
It was found that ?-stabilizers have a twofold greater contribution to elemental partition as compared to ?-stabilizers. The composition and the width of the ?/? interface were found to have a great impact on the mechanical properties of the alloy.
The phase transformation and element partitioning behavior during martensite breakdown were revealed in this work by a thorough compositional and microstructural investigation that was carried out at the bulk and atomic scales and is connected with mechanical characteristics.
Prof. N. K. Mukhopadhyay, from the Department of Metallurgical Engineering, Indian Institute of Technology (BHU), Varanasi, India, appreciated the work done by the authors, and recognized its importance with regard to current emerging materials with the following comments: “As additive manufacturing has taken its own rightful place as an alternative source of product development in niche areas, the components produced need to exhibit the robustness and desired service lifetime which is still under active assessment.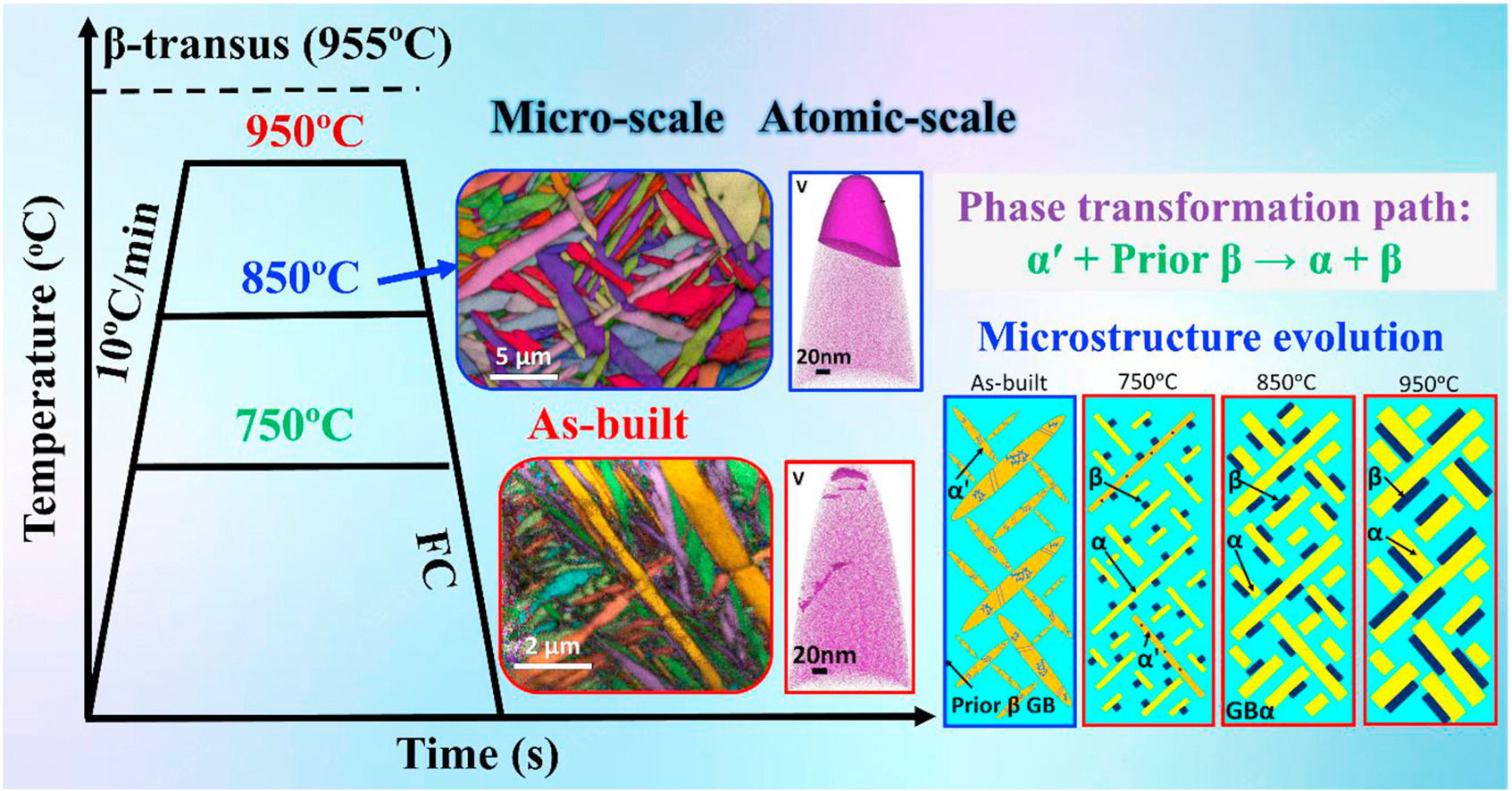
To this extent, the publication by Usha Rani et al. on the microstructural evolution in additively manufactured Ti-6Al-4V alloy upon thermal processing, has provided deeper insights. Especially the analysis at atomic scale highlighting the role of each constituent element and their mobility (atomic jump!) during the exposure to different conditions; their attraction to multi-dimensional defect sites inducing the local phase change which affects the mechanical properties are worth noting.
The choice of techniques employed in this study to understand the atomic-scale phenomena inducing discernible changes at micron scale and the resultant consequential effects on the mechanical properties are highly commendable. Overall, this publication is a very well-structured piece of work, highly appropriate for the present scenario of emerging materials manufacturing, advancing the field of study by unearthing details which otherwise are rarely investigated. All the above, signifies the high degree of competence prevalent in this research team and their scientific understanding presented in this study has demonstrated the unique kind of world class research activity emerging from Indian shores!”
The Article is Written by Akshay Anantharaman | To Read the Complete Article, CLICK HERE
S. Usha Rani: Writing – review & editing, Writing – original draft, Methodology, Investigation, Conceptualization. M. Sadhasivam: Validation, Investigation, Formal analysis. D. Kesavan: Supervision, Methodology, Investigation. K.G. Pradeep: Supervision, Methodology, Investigation, Conceptualization. M. Kamaraj: Supervision, Methodology, Investigation, Conceptualization.