The Sennheiser Group is making large investments in its own facilities. By doing this, the family-run business is securing the autonomy of its output and guaranteeing its continuous prosperity in influencing the audio industry’s future.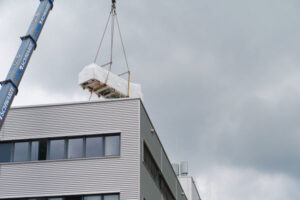
Modern production methods are now being invested in at its headquarters in Wedemark, close to Hanover, especially printed circuit board assembly.
‘Moving into the Future’ is the umbrella term for a number of growth and restructuring initiatives underway. To create room, the first step was to move an existing production line. Then a crane was used to hoist two brand-new reflow ovens through the manufacturing hall’s roof.
Sennheiser is further expanding its production capacity at its headquarters in Germany. Within production, the relocation of ‘Surface Mounted Device (SMD) Line 1’ to create space for additional printed circuit board assembly systems was only the beginning.
“The relocation of this production line system and the additional installation of new ones is one of several measures to strengthen our production. By continuous investments in the production capacities at the Wedemark site, we are making ourselves more independent of supply chains. In the past year, we have already invested around 5 million euros here on site. This year, it is more than 14 million euros,” explains Dr. Andreas Fischer, Chief Operating Officer (COO) and member of the Executive Management Board. “We have been constantly improving our supply chains and continuously expanding our own production capacities. This not only makes us future-proof for the long term, but also ensures we continue to be a reliable partner for our customers,” adds Co-CEO Daniel Sennheiser.
Currently operating at the Wedemark location since 2017, the initial SMD 1 production line was replaced in 2022 by a second line with double the production capacity. When combined, they can consistently assemble printed circuit boards on a line.
The SMD 1 system installs components at an average rate of 25,000 pieces per hour on a printed circuit board with the assistance of eight placement heads. Two SMD placement systems were previously available on the manufacturing floor; however, with the machine’s relocation, there is now room for four.
With the arrival of the reflow ovens of the new lines, the company can not only increase its printed circuit board production capacity several times over, but also keep pace with technological developments. The new setup also allows for an optimized material flow. The logistics of such a move are challenging and a special structure had to be built to transport the huge parts of the machine.
To install the reflow ovens, the roof of the production hall had to be opened and the ovens were placed in the production area from above using a crane. The fact that everything went smoothly is mainly due to the extensive preparation beforehand, says Fischer. “Since the beginning of the year, we pre-produced around 10,000 printed circuit boards to compensate for the loss of production during the move. Without the dedicated commitment of the entire team, the relocation would not have been possible.”
Moving into the Future
This action is a component of a larger investment plan to fortify the Wedemark facility. The Wennebostel location specializes in high-precision automated procedures and luxury product manufacturing, which includes creating microphone capsules in a dedicated clean room.
The business made investments in ten more manufacturing systems for microphone components in 2023, a digital tool management system, and a new SMD line in 2022 in order to narrow this emphasis. The implementation of an automated SMD storage system is one of the other impending actions.
The plant in Bra?ov, Romania, on the other hand, focuses on manual production as well as the final testing and packaging of products. The audio specialist is also investing significantly in this location as part of its sustainable growth strategy and tripled the available production space last year.
In 2023, a total of almost 13 million euros went into the expansion of the company’s own production sites. “With our own strong production facilities, we are investing in our core competence – in the high quality of our products,” says Andreas Fischer.