A yield management system is meant to help semiconductor companies increase yields and accelerate time to market by saving them time and money.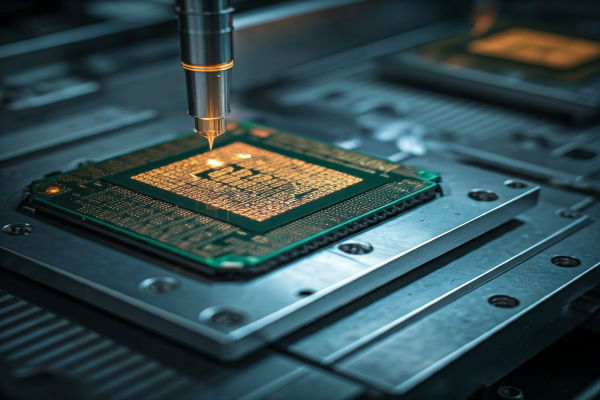
Specialized equipment and software are needed for semiconductor yield management systems in order to track, evaluate, and improve the production process. To exploit and maximize the available data, these also require skilled workforce.
Defect inspection instruments, for instance, assist in scanning wafers at different phases of the procedure. It makes it possible to find physical flaws. Similarly, as part of failure analysis, Scanning Electron Microscopes (SEMs) offer high-resolution imaging to identify and examine flaws that are not achievable with defect inspection equipment.
A faultless yield management program that can synchronize with Automated Test Equipment (ATE) to collect, process, and analyze large volumes of data is required during the testing phases.
This end-to-end data is essential for guaranteeing that the wafer’s yield meets specifications, and YMS tools include a number of features to make the review process easier in the event that there are any deviations or problems during testing.
Similar to YMS, statistical process control (SPC) software is also available to guarantee that the process stays within predetermined bounds in real time. Furthermore, a lot of SPC programs offer various criteria that can really detect test-driven deviations during silicon wafer testing.
The production of semiconductor devices is a multi-step, extremely complex process. Deviations from these procedures, no matter how small, can lead to flaws that make the device unusable.
In order to guarantee that the devices produced are of the appropriate quality and functionality, semiconductor yield management is a procedure that seeks to detect and resolve yield difficulties. Its primary objective is to increase yield by reducing the quantity of faulty devices and streamlining the production process to increase efficiency.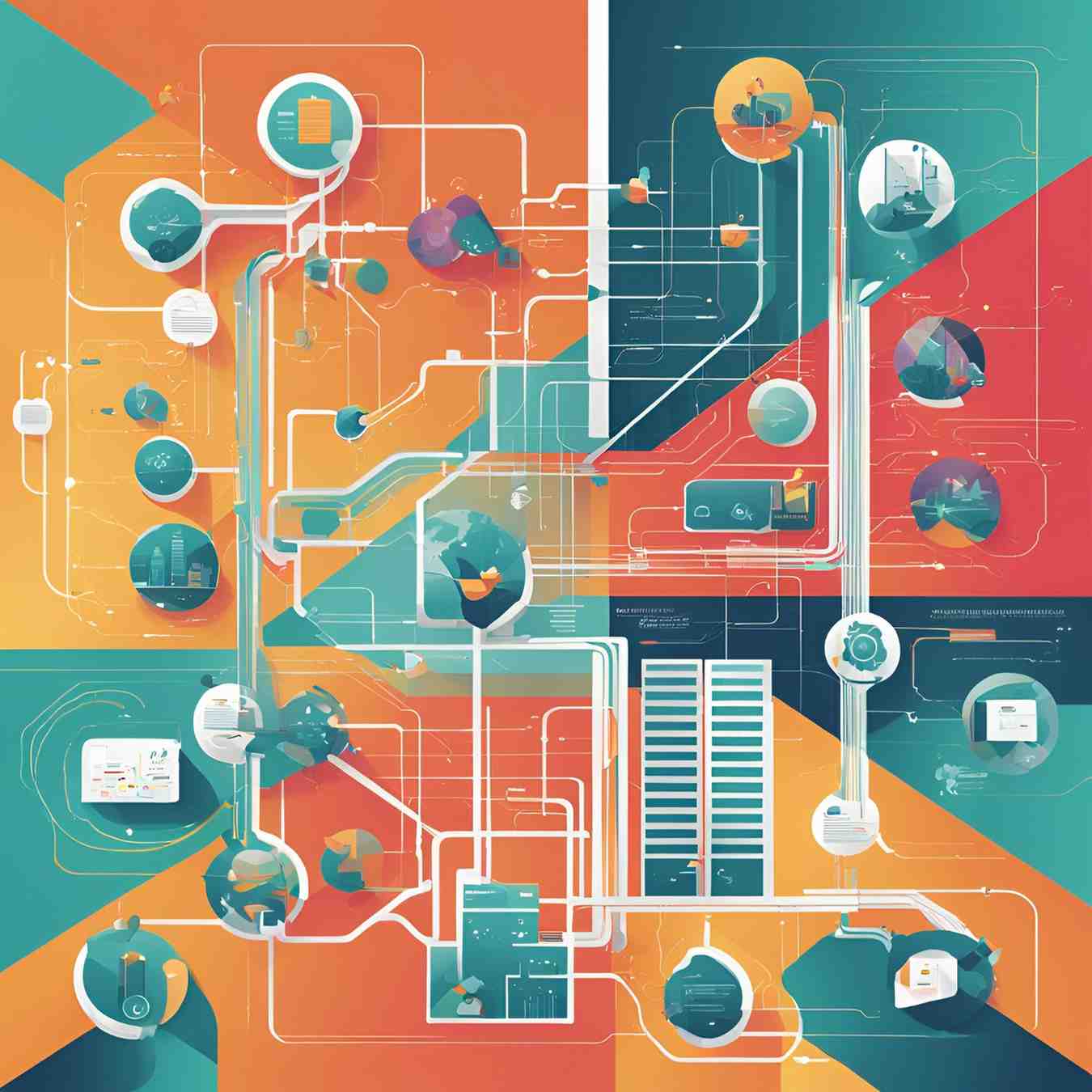
Semiconductor yield management system is a complex field that blends technical know-how with critical thinking and people abilities.
From manual inspections and crude data analysis in the past to sophisticated real-time monitoring and advanced analytics in the present, semiconductor yield management has changed with time.
Yield management system is frequently thought to be limited to silicon test results. It is far more than that in practice. It involves making sure that a yield monitoring procedure is included at every process step, from wafer startup to the last packing stage.
In this article, let’s examine the necessity, difficulties, potential, and prospects of yield management.
Understanding Programming Languages: Analyzing vast volumes of data to find trends, anomalies, and possible reasons for flaws is known as yield management. Experts in this area need to be adept at analyzing data, applying statistical software, and extracting useful information from intricate datasets. Another benefit is being able to create automated tools in a variety of programming languages.
How To Connect The Anomalies: Defects can result from even the smallest deviation in the thousands of complex procedures involved in semiconductor manufacturing. To spot and fix small inconsistencies that others might miss, one must have an acute eye for detail. To provide a great conclusion, it is also essential to comprehend several sets of fabrication process phases and know how to connect the irregularities.
Communication and Collaboration: Effective communication is essential for interdisciplinary teams of yield management experts to share findings, make suggestions for enhancements, and guarantee that remedial actions are taken. Enhancing yield requires teamwork. To increase yield, specialists from different functions must work together.
Timely and Informed Decisions: Professionals in yield management must balance the trade-offs between quality, cost, and production speed in order to make prompt and well-informed decisions based on the abundance of data.
Transition Towards Cloud, AI, Hurdles And Future:
Due to disaggregated tools and equipment, semiconductor end-to-end data analysis has historically been expensive in addition to being difficult to gather. The necessity to implement an appropriate hardware and software system that can enable end-to-end data collecting is the reason for the high cost.
The cloud and AI approach has not yet been adopted by many yield management flows in the semiconductor sector. Furthermore, as the use of AI grows, it is now essential for semiconductor businesses to move toward or accept cloud solutions in addition to embracing AI solutions to guarantee that the AI features can be created at scale, as the two go hand in hand.
Cloud Platforms: Data collected during manufacture has increased dramatically due to the growing complexity of semiconductor designs and processes. Cloud technologies provide easy access to data across international manufacturing sites and provide enormous storage capacities. Faster decision-making and real-time data processing are made possible by this centralization. In order to guarantee that yield optimization techniques are uniform across facilities, semiconductor engineers and data scientists from several locations can concurrently evaluate data, discuss discoveries, and put solutions into action.
AI Algorithms: AI systems can use historical data to forecast possible yield problems. By taking a proactive stance, producers may deal with possible issues before they arise, guaranteeing increased yields. Conventional techniques can take a lot of time. AI speeds up the troubleshooting process by rapidly sorting through large datasets to identify the underlying causes of flaws.
A future with increased yields, lower manufacturing costs, and quicker time-to-market is promised by the mingling of cloud computing and artificial intelligence in semiconductor yield management.
One may anticipate a more streamlined, effective, and responsive semiconductor production environment as these technologies advance and the sector gets past its early challenges.
As proactive yield optimization replaces reactive problem-solving, a new era of superior semiconductor production will begin.
Overcoming Hurdles on ROI and TCO
The substantial initial outlay needed to implement semiconductor yield management technology is a considerable barrier to entry for small and medium-sized semiconductor manufacturers or newcomers to the market.
Businesses must carefully weigh the upfront expenses against the anticipated return on investment (ROI) when evaluating semiconductor yield management systems.
Additionally, during the course of the software’s lifecycle, semiconductor businesses must take into account the total cost of ownership (TCO), which includes continuing maintenance, upgrades, support, training, and integration costs. The overall viability and affordability of using yield management systems may be greatly impacted by these extra expenses.
Future With Subscription-Based Models
Businesses can investigate a range of options. One example of this is flexible pricing schemes, which For semiconductor companies with limited funds, yield management software suppliers can give flexible pricing structures including pay-per-use or subscription-based models.
This enables companies to scale up as their operations expand and pay for the software according to consumption.
Furthermore, yield management software vendors may help semiconductor companies perform thorough ROI evaluations that clearly illustrate the possible advantages and cost reductions related to putting the technology into practice. Businesses can use this to advocate for their investment in yield management solutions and make well-informed decisions.
References: CLICK HERE