By Jeff Shepard | Contributed By DigiKey’s North American Editors
The increasing complexity of Industry 4.0 factory and logistics automation requires new approaches to system design that simultaneously maximize safety and productivity.
The flexible nature of Industry 4.0 operations means that the placement and extent of hazardous operations can change occasionally, and safety systems must adapt quickly. A reconfigurable, programmable, and flexible safety system is needed.
The ability to establish warning zones to alert workers approaching a hazardous area before they get too close can be a big plus. It prevents workers from accidentally entering the hazardous area, tripping a safety device, and turning off a machine. That enhances uptime and productivity.
This article begins with a brief review of international standards for safety mats and safety laser scanners, then moves on to comparing application considerations for safety mats and safety laser scanners, looking at factors like contact versus non-contact operation, warning field protection, and adjustability.
It closes by presenting examples of miniature safety laser scanners from SICK and how they meet the requirements of several applications, along with installation and configuration options, including how the scanners are easily replaced if they become damaged.
Key safety performance standards include International Electrotechnical Commission (IEC) 61508, “Functional Safety of Electrical/Electronic/Programmable Electronic Safety-related Systems (E/E/PE, or E/E/PES),” International Organization for Standardization (ISO) 13849, “Safety of machinery — Safety-related parts of control systems,” and IEC 61496, “Safety of machinery — Electrosensitive protective equipment.”
Safety mats and safety laser scanners meet various parts of those standards. For example, IEC 61508 defines a series of safety integrity levels (SILs). Safety laser scanners meet SIL 2 requirements. So do some, but not all, safety mats. Some safety mats only meet the requirements of SIL 1, which is an order of magnitude less stringent than SIL 2.
SIL 1 safety devices are intended for use with low-risk applications where the consequences of a failure are not severe, like basic machine guarding, non-critical processes, and simple alarms. SIL 2 safety devices are designed to mitigate risks that could result in serious injuries or significant environmental damage, but not necessarily catastrophic events.
Using similar concepts to SILs, ISO 13849 defines performance levels (PLs). Safety mats typically qualify for a PLc certification, while safety laser scanners must qualify for the tougher PLd certification. Some safety mat installations can also meet PLd performance requirements.
To become certified, a safety laser scanner must meet SIL 2, PLd, and IEC 61496-3, specifically covering active optoelectronic protective devices responsive to diffuse reflection (AOPDDR, or laser scanners). The implications of the various safety certifications for safety mats and safety laser scanners are important, but they are just the start when maximizing protection and productivity.
More to consider
Properly specified safety mats and safety laser scanners can both meet the IEC and ISO safety requirements. But that’s not the end of the story; there’s more to consider in Industry 4.0 factory and logistics automation applications.
A safety mat is a matrix of mechanical switches. When a weight, like a person stepping on the mat, closes one or more of the switches, it sends a signal to the mat controller that stops the operation of the protected system.
The mechanical nature of safety mats can be a cause for concern. First, for the mat to operate, there must be direct contact with a person walking across the mat. Second, the mats are subjected to wear and (sometimes literally) tear. People can drop heavy and/or sharp tools on the mat, damaging it (Figure 1). Or a forklift may drive across the mat and damage it. Environmental factors like spills of corrosive materials can also compromise the mat.
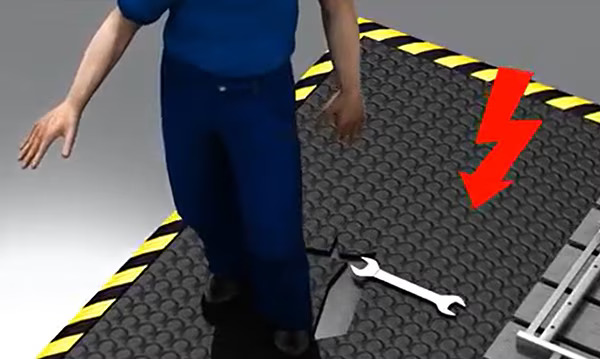
Adjustability
Safety mats are inherently fixed installations and are not adjustable. There are different sizes and mat configurations for specific installation requirements. That can present challenges in Industry 4.0 factories and logistics operations that are subject to reconfiguration as process demands change.
Making changes to safety mat-based systems can require the acquisition of a new mat, extending the time needed for the changeover to become operational. That can negatively impact machine availability and overall productivity.
One way to minimize the impact is to keep various replacement safety mat sizes on hand. That can speed changeovers and the replacement of mats that become damaged. But it’s also expensive. It can also require keeping a variety of safety mat controllers on hand since not all mats are compatible with all controllers.
These issues can be addressed by using safety laser scanners. Safety laser scanners are not based on mechanical switches; they are electronic devices that can be adjusted for various application needs.
Safety laser scanners are a non-contact technology that use an infrared (IR) laser to scan the surroundings in two dimensions. They emit short pulses of IR light. If a pulse of light strikes an object, it’s reflected to the scanner. The distance to the object can be determined with a high degree of accuracy based on the time interval between the moment of transmission and the time the reflected light returns.
The ability to determine the distance to obstacles enables safety laser scanners to establish a series of warning and protective fields based on the nearness of an object. Some safety laser scanners can have dozens of defined fields. That can be useful for applications like navigation for an autonomous mobile robot.
The S300 Mini Standard safety laser scanners from SICK are optimized for safety applications that need three defined fields — a protective field and two warning fields — to be active simultaneously. Their compact dimensions of 102 x 116 x 105 millimeters (mm) (w x h x d) make them suitable for applications like robotic work cells and automatic guided vehicles (AGVs) (Figure 2).
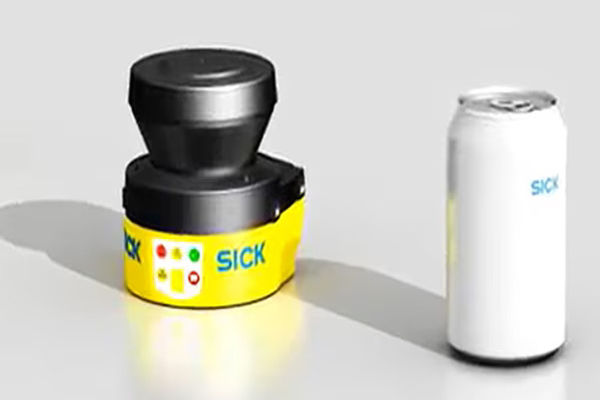
S300 Mini Standard scanners have a 270° scan angle to cover a wide area and a selectable resolution for hand, leg, or body detection. These scanners support warning field ranges up to 8 m and are available with three maximum protective field ranges:
Dynamic environments
Dynamic environments, where the layout or operational conditions change or where AGVs move around, can benefit from configurable safety laser scanners. The detection zones can be modified as needed to suit changing protection needs.
Setting multiple warning fields can be especially useful for preventing people from getting too close and shutting down a machine. The warning signal devices can include a simple flashing light if the first warning field is breached and a warning siren or horn if the second warning field is entered. There are specific rules for calculating the size of protection fields.
Safety Distance Calculations
ISO Standard 13855, “Safety of machinery – Positioning of safeguards with respect to the approach of the human body , includes guidelines for calculating the minimum safe distance required to stop a machine when a person approaches it. ISO 13855 applies to several types of safety devices, including safety laser scanners, safety light curtains, pressure-sensitive devices, safety mats and floors, and more.
It can be useful when calculating the size of safety fields for safety laser scanners (Figure 3). A common formula for calculating the safe distance, S, is S = (K × (TM + TS)) + ZG + ZR + CRO, where:
- K = Approach speed (1,600 mm/s, defined in ISO 13855)
- TM = Stopping time of the machine or system
- TS = Response time of the safety laser scanner and the downstream controller
- ZG = General supplement = 100 mm
- ZR = Supplement for reflection-related measurement errors
CRO = Supplement to prevent reaching over
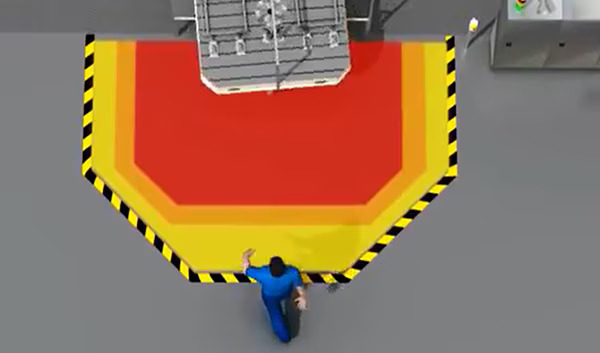
Automated guided vehicles
Automated guided vehicles (AGVs) move items quickly and efficiently without human intervention in Industry 4.0 factories, warehouses, and distribution centers. In some AGVs, switching strips or bumpers are used to detect obstacles.
That can limit the speed of travel for the AGV, and the strips or bumpers can experience physical damage, requiring replacement and taking the AGV out of operation for a period.
To maintain safety, flexibility, and maximum availability, AGVs can replace switching strips and bumpers as the primary safety devices, and they can include a laser safety scanner to detect obstacles and safely stop. The small size of the S300 Mini facilitates integration, even in the smallest AGVs (Figure 4).
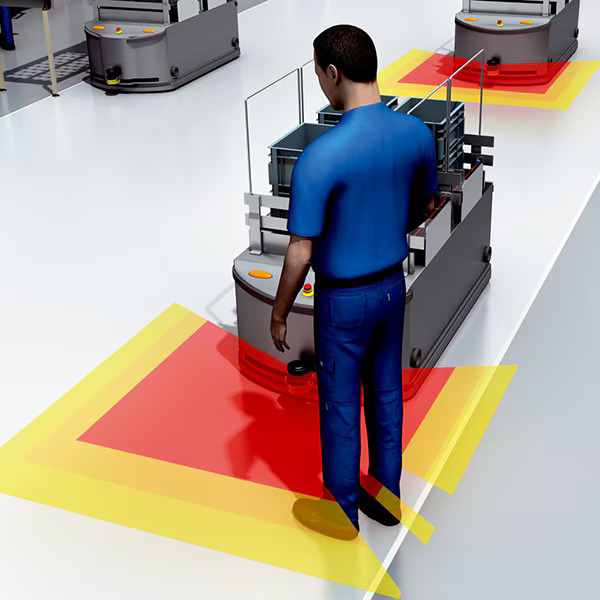
Using two safety laser scanners can provide an expanded protected area. If the scanners are mounted on the front corners of the AGV, the protected area extends to the front and both sides of the vehicle.
Suppose the scanners are mounted diagonally opposite each other on the front and rear of the vehicle. In that case, the protected area will surround all sides of the AGV, enabling safe movement in both directions.
Configuration, installation, and maintenance
Configuration and diagnostic software (CDS) from SICK can be used to define protective and warning fields using a PC or laptop.
The software includes an intuitive interface for application design and implementation. The software also calculates and saves all configuration and diagnostic data for quick commissioning and/or efficient troubleshooting. Configuration and diagnostics can be implemented during commissioning or maintenance.
SICK also offers a choice of mounting kits for physically attaching the S300 Mini safety laser scanners.
Kit 1a, model 2034324, is the basic mounting bracket without a protective cover for the optics, and kit 1b, model 2034325, includes optics protection (Figure 5). In addition, supplemental mounting brackets, including kit 2, model 2039302, and kit 3, model 2039303, can be added to align the scanners in two planes. The maximum adjustment angle is ± 11° in both planes.
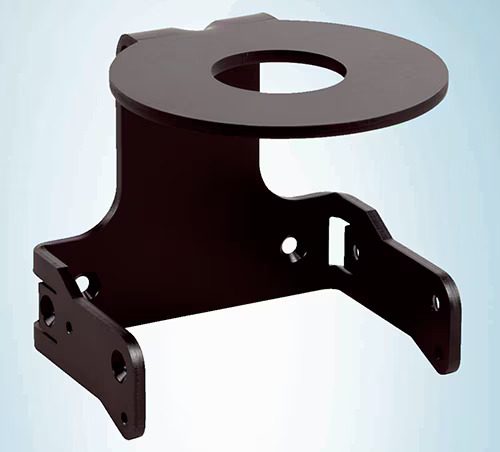
The mounting kits also support quick replacement of damaged scanner heads. The replacement scanner head attaches to the system plug, which is permanently mounted on the machine.
The replacement head immediately downloads the configuration data from the system plug and assumes the programmed safety tasks, no reprogramming or manual downloading of configuration data. It’s a plug-and-play process that minimizes machine downtime.
Summary
S300 Mini Standard safety laser scanners provide a robust alternative to safety mats in Industry 4.0 factories, warehouses, and distribution centers that simultaneously maximize safety and productivity.
They meet IEC 61508, ISO 13849, and IEC 61496 safety standards and are suitable for fixed installations and mobile platforms like AGVs. Finally, S300 Mini Standard safety laser scanners support flexible and rapid configuration, installation, and maintenance.
About this author
Jeff has been writing about power electronics, electronic components, and other technology topics for over 30 years. He started writing about power electronics as a Senior Editor at EETimes. He subsequently founded Powertechniques, a power electronics design magazine, and later founded Darnell Group, a global power electronics research and publishing firm. Among its activities, Darnell Group published PowerPulse.net, which provided daily news for the global power electronics engineering community. He is the author of a switch-mode power supply text book, titled “Power Supplies,” published by the Reston division of Prentice Hall.
Jeff also co-founded Jeta Power Systems, a maker of high-wattage switching power supplies, which was acquired by Computer Products. Jeff is also an inventor, having his name is on 17 U.S. patents in the fields of thermal energy harvesting and optical metamaterials and is an industry source and frequent speaker on global trends in power electronics. He has a Masters Degree in Quantitative Methods and Mathematics from the University of California.