Switching regulator topologies are preferred for most general-purpose power conversion applications as they combine high efficiency with design flexibility. As a result, many switching topologies have been developed to suit a wide range of applications.
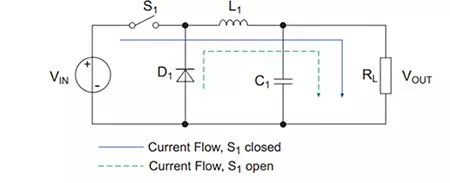
Figure 1 shows the principle of operation of the buck converter. Inductor L1 and capacitor C1 can be considered as an LC low pass filter. When switch S1 is closed, the voltage VL1 across load RL slowly ramps up as C1 charges up through L1.
If S1 is then opened, the energy stored in the magnetic field of the inductor is clamped to 0V at the switch end of the inductor by diode D1, so the energy has no choice but to discharge into the capacitor and load, causing the voltage across the load to slowly ramp down.
The average output voltage is then the duty cycle of the PWM control signal multiplied by the input voltage VIN. Figure 2 shows the characteristic waveforms of this circuit.
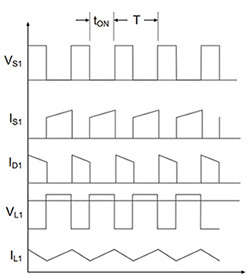
The simplified circuit in Figure 1 may be expanded and refined as shown in Figure 3.
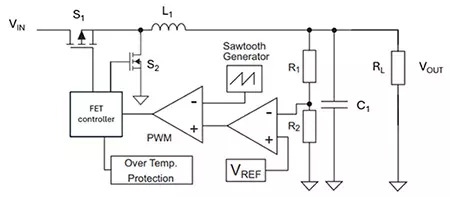
This circuit includes a feedback circuit that compares VOUT to a reference voltage VREF and adjusts the PWM duty cycle accordingly. The voltage divider formed by R1 and R2 sets the desired output voltage. The circuit also replaces diode D1 in Figure 1 with MOSFET S2 that is turned on by the controller only when needed for correct operation, forming a synchronous rectifier.
This approach increases the conversion efficiency at the cost of extra complexity. RECOM’s DC/DC Book of Knowledge discusses switching converter topologies and design tradeoffs in great detail.
Buck regulator advantages and disadvantages
The buck regulator topology has several advantages and disadvantages compared to other power conversion topologies.
Advantages include:
- High Efficiency: Buck converters can achieve high efficiency, often exceeding 97%. This efficiency is especially achievable in synchronous designs.
- Wide Input Voltage Range: Buck converters can handle a wide range of input voltages.
- Compact Design: They require minimal external components, making them suitable for space-constrained applications.
- Flexible Output Voltage: The output voltage can be set anywhere within a wide range.
Disadvantages of buck switching regulators include:
- Slow Response to Load Changes: Current mode buck converters respond relatively slowly to sudden load changes, especially at low duty cycles. Once the power transistor S1 switches off, it remains off until the next clock cycle.
- Output Voltage Fluctuation: Fast load changes can lead to significant output voltage fluctuations due to limited bandwidth.
- Noise Filtering Challenges: The buck regulator generates EMI due to the pulsed input current caused by the switching operation. Noise filtering is necessary.
Buck converters offer efficiency and compactness but have limitations related to load response, noise, and inductor selection.
RECOM’s RPH family simplifies buck regulator design
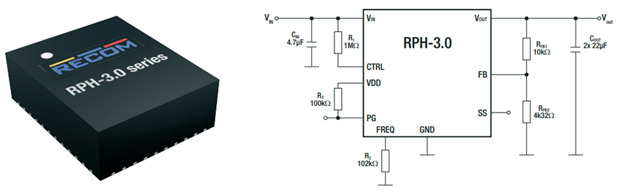
The RPH-3.0 series is a compact and versatile solution designed to meet challenging power conversion needs with efficiency and precision.
This buck regulator power module includes an integrated shielded inductor for low EMI and offers a host of features to ensure optimal performance and reliability. With a maximum input voltage of 55V, this module provides a robust solution for various applications, ensuring stable and efficient voltage regulation. The output voltage is fully programmable within the range of 1 to 15V, providing flexibility to meet specific system requirements.
Delivering up to 3A maximum output current, this power module is well-suited for powering a range of electronic devices and systems. The RPH series comes equipped with Short Circuit Protection (SCP), Overcurrent Protection (OCP), Overvoltage Protection (OVP), and Undervoltage Lockout (UVLO) features, ensuring the longevity and protection of connected devices.
The compact 10mm x 12mm x 4mm QFN package makes the RPH power module ideal for applications with space constraints, allowing for easy integration. The use of Flip-Chip technology enhances thermal management, ensuring that the module operates efficiently even in demanding conditions. The RPH features an efficiency rating of up to 91%; this high efficiency not only contributes to reduced energy consumption but also minimizes heat generation, enhancing the overall reliability and lifespan of the module.
The RPH-3.0 series is a state-of-the-art solution that combines cutting-edge technology with compact design and robust protection features for all consumer electronics, industrial applications, or any other project requiring a reliable point of load supply that delivers consistent and efficient performance.
A power module based on the buck topology is non-isolated, i.e., it does not use a transformer to provide galvanic isolation between input and output. Many applications in data acquisition, the industrial Internet of Things (IIoT), green energy, and other fields call for galvanic isolation. RECOM offers a wide range of isolated power modules for these applications.