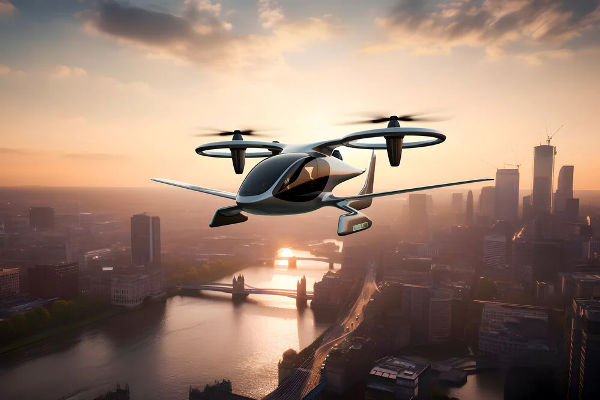
Experts have been talking about the eventual arrival of urban air mobility (UAM) vehicles, often called flying cars, for almost as long as there have been cars, and we are still waiting for those predictions to become true. Apart from a few prototypes and promises, there has not been much progress of any substance until now.
With roads becoming more congested, especially in cities, there’s never been a better time to introduce UAM. Today, several companies have working prototypes, many of which are in the certification process from national aviation bodies.
Some UAM designs require trained pilots, such as the VoloCity air taxi, which was designed by the German company Volocopter. Other designs will be autonomous, like the EHang EH216-S aircraft from China. Both of these UAM vehicles have already undergone in-depth testing and trial flights. Most current UAM designs will be expensive and intended for commercial use in applications like air taxis. However, in the not-too-distant future, mass-market personal UAM will become more viable.
Over the last decade, progress has been made in all the critical technologies required to bring down the barriers to developing more cost-effective UAM.
Most of these advancements have not been specifically targeted at UAM use but come from developing EVs (Figure 1), as well as commercial and military drones. This blog examines the most important technologies for UAM development and considers how they will enable future advancements.
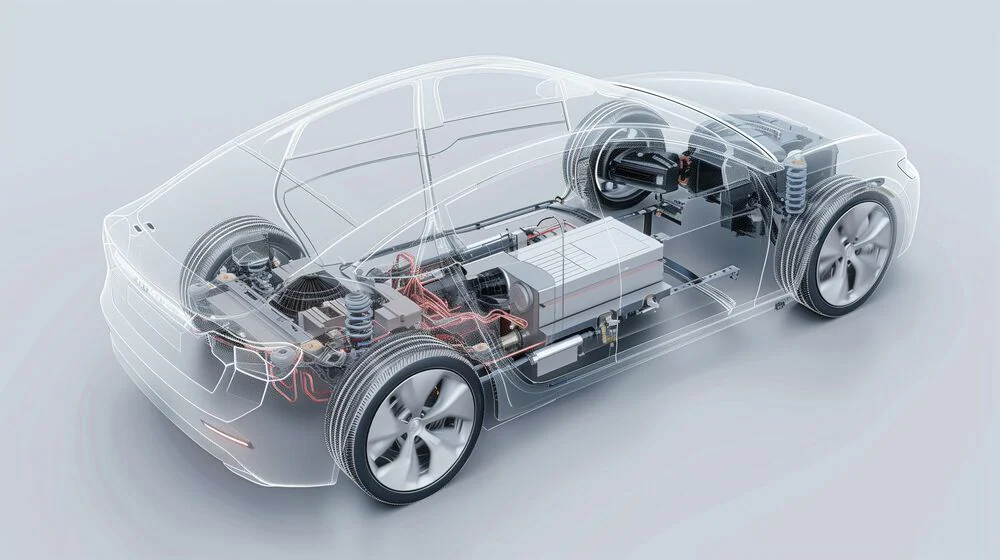
Motors
One of the most important metrics in flight applications is the power-to-weight ratio. This applies even more to motors, as designs like the VoloCity air taxi have 18 rotors that each require a motor. Over the last few years, advances have been made in both motor performance and weight reduction.
One innovation that is of great interest to UAM manufacturers is axial motors. These motors have magnetic flux parallel to the axis of rotation instead of perpendicular, as found in existing radial flux motors.
Axial motors are more efficient and compact, feature power densities above 6kW/kg, and are light weight. Another exciting innovation in motors is the in-wheel motors developed for EVs to control the vehicle’s wheels independently and precisely while reducing weight and space. This technique could be used to provide UAM vehicles with independent rotor control.
As for the type of motor used, switched reluctance motors (SRMs) are emerging as a popular solution for automotive applications.[1] SRMs offer high-speed operation, efficiency over a wide speed/torque range, heat and vibration tolerance, and a high power density.
The technology’s previous drawbacks, including torque ripple and acoustic noise, can now be overcome through improved design and control. Another massive benefit of SRMs is that they don’t require rare-earth elements in their construction, which reduces cost and provides a more straightforward supply chain.
A second type of motor widely used in smaller EVs that could be adapted for UAM design is the synchronous reluctance motor-internal permanent magnet (SynRM-IPM) hybrid design. As UAM vehicles are usually propelled by multiple rotors, the advantages of SynRM-IPM designs include their small size, high torque, high efficiency, and minimal back electromotive force (EMF) drag, which helps eliminate high-speed inefficiencies.
Battery Technologies
Batteries will provide the power for UAM vehicles. The Li-ion batteries we use today tend to be heavier than they need to be, as they are normally encased in a thick metal prismatic or cylindrical casing, but they still offer the best power-to-weight ratio we currently possess. However, solid-state Li-ion batteries should be entering the market soon, and they will provide an improved power-to-weight ratio as well as higher levels of safety. Samsung SDI plans to mass produce solid-state batteries by 2027.[2]
The company’s ASB battery will have an energy density of 900Wh/L, which is over 40 percent more dense than the company’s current P5 prismatic Li-ion battery. Other automotive companies, including Toyota and Volkswagen, are targeting similar timelines for their own solid-state batteries.
Solid-state batteries don’t need a thick metal casing since their solid-state electrolyte cannot leak, and they are much less prone to self-combustion. In urban environments, mileage might not be as crucial as in other areas. This means that solid-state battery packs for UAM designs can be smaller, safer, and lighter while still providing sufficient range (Figure 2).
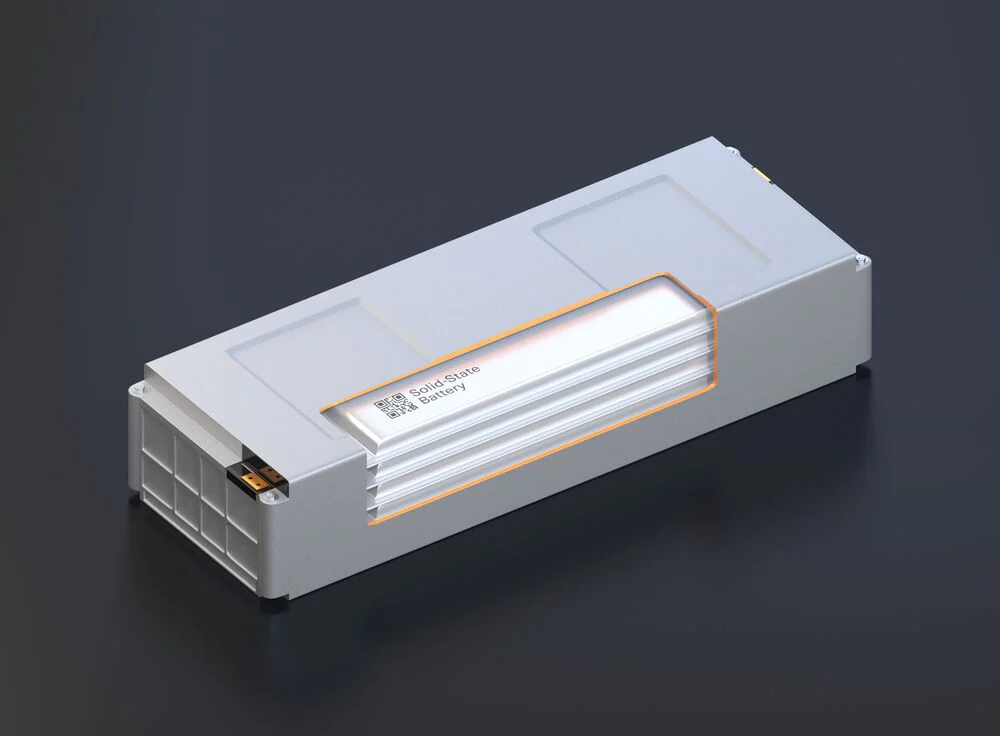
Architecture
The automotive industry is in the process of migrating from a distributed architecture to a more centralized one with zonal control to reduce weight and complexity. As both of these issues are also major challenges to UAM manufacturers, the changes currently being made in the automotive industry will also provide the inspiration for UAM designs in the future.
The number of automotive electronic control units (ECUs) in a distributed automotive system has risen dramatically, with around 100 ECUs in an average vehicle.[3] These ECUs use much of the vehicle’s power and require extensive wiring to communicate with each other. Wiring is heavy, with an estimated 100 to 120lbs of wire harness weight in an average vehicle.[4]
The centralized architecture has a powerful main control unit that only needs to communicate with a single ECU for each vehicle zone, reducing the required wiring and, correspondingly, the vehicle’s overall weight. Another benefit of having a robust central computing platform is that it can run AI applications, which will also be necessary for UAM designs.
At the same time, the industry is moving from 400V architecture to 800V to provide faster charging times, improved performance, reduced weight, and better battery life. 800V architecture uses lower currents, which allow thinner, lighter wiring and produce less heat, reducing stress on the battery and lowering the chance of thermal runaway. A 48V bus voltage is also being adopted in EVs for many of the same reasons. These new voltage levels can provide similar benefits to UAM manufacturers.
Powertrain
Wide-bandgap (WBG) materials have revolutionized EV powertrains, and they hold the same potential for UAM vehicles.
Compared to silicon, silicon carbide (SiC) and gallium nitride (GaN) components provide superior performance, better efficiency, higher switching frequencies, and higher operating temperatures.
High-speed switching allows the use of smaller magnetics, reducing the size and weight of the overall solution, and higher efficiency means more of the stored power is used effectively, while less heat is generated. SiC components are also very rugged and feature high thermal resistance, so they last longer and dissipate heat better.
Operating Safety
While pre-approved flight plans should ensure that UAM vehicles never come close to one another or any other object, there are still dangers for several reasons, technical or otherwise. Fortunately, autonomous vehicle innovation has provided a solution with a combination of optical, radar, and lidar technologies that give a 360° view of the vehicle.
These technologies have been under development for quite some time and are well understood, and they should be able to operate even more accurately in the air where any object is a threat.
Autonomous unmanned drones have already been tested by companies, such as Amazon,[5] using some or all of these technologies (Figure 3).
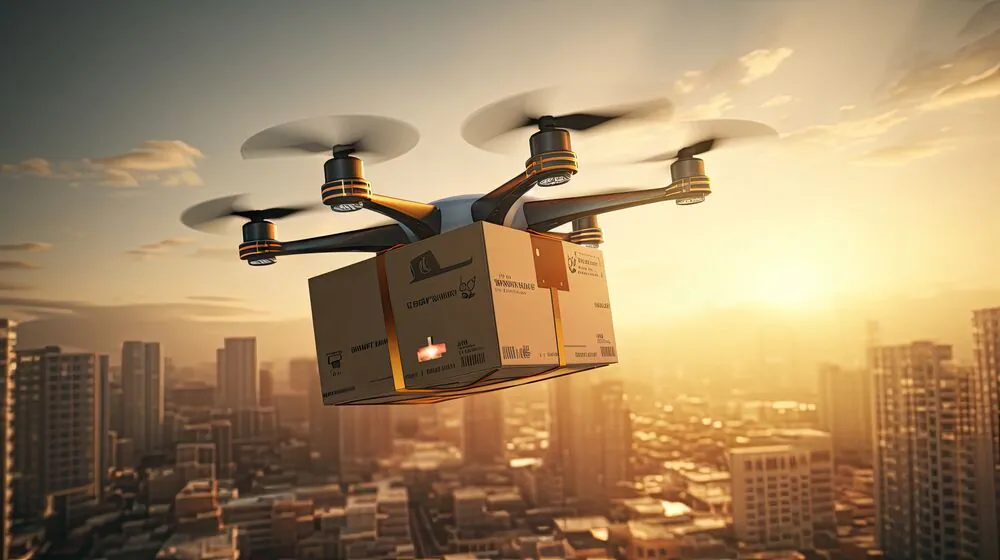
Navigation
Most, if not all, UAM designs will rely heavily on global navigation satellite systems (GNSS) for navigation. In urban environments, signals can get blocked or reflected by tall buildings, and outages and malfunctions are always a danger with technology.
Electronic components, in the form of internal measurement units (IMUs) and other sensors—such as cameras, lidar, and odometers—can improve the accuracy and reliability of the GNSS system or even take over navigation for a period if there is an outage.
Conclusion
We may not see personal UAM vehicles arrive imminently, but the main technological ingredients are either currently available or will be very shortly.
The development of EVs and autonomous vehicles has done the hard work on most of those technologies, while advancements in drone technology have also helped considerably.
Likely, today’s futurologist predictions on the introduction of flying cars will soon be the ones that come to pass.
ABOUT THE AUTHOR
Since graduating with a BSc in Electronic Systems from the University of the West of Scotland in 1997, Alistair Winning has worked in electronics media across marketing, PR, and journalism roles. During that time, he worked as the editor of Electronics Engineering, Embedded Systems Europe, EENews Embedded, Technology First, Electronic Product Design and Test, and Panel Building and Systems Integration magazines. Currently, Allistair is the European Editor of Power Systems Design and a freelance writer, specializing in electronics and engineering.
This article is originally sourced from Mouser Electronics.