With its new MAX OLED platform, Applied Materials has shown a revolutionary advancement in OLED display technology. High-quality displays will be possible on a wider variety of devices, such as PCs and TVs, thanks to this invention, which is expected to redefine the scalability and efficiency of OLED manufacturing.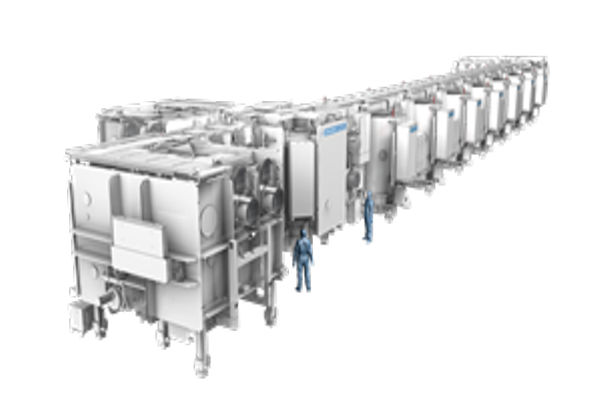
It is said that switching from Gen 6 to Gen 8 glass substrates for OLED manufacture is the main breakthrough. Because Gen 8 substrates offer improved yield efficiency and optimize the number of displays produced per sheet of glass, this change enables manufacturers to make larger and more affordable OLED panels. The increasing need for bigger and more functional screens, particularly in consumer devices like laptops and tablets, is directly met by this scalability.
Additionally, MAX OLED technology promises notable enhancements in display performance. Compared to conventional OLED displays, panels made with this method are said to have a 5x longer lifespan, 2.5x higher resolution, and up to 3x brighter brightness. Furthermore, these improvements are made while using 30% less power, which makes the technology more ecologically friendly and energy-efficient.
The platform overcomes old obstacles in OLED manufacturing, like homogeneity and material waste, by integrating new materials and precision engineering techniques. The accuracy of material deposition is improved by its special co-evaporation technique, and production workflows are streamlined by proprietary tools. MAX OLED minimizes its impact on the environment and lowers expenses by optimizing material consumption.
The display business is changing as a result of the adoption of this new technology by top display manufacturers such as Visionox, Japan Display, and Samsung Display. Beyond high-end smartphones and TVs, OLED adoption may grow thanks to the capacity to mass produce affordable, high-quality OLED screens.
Customers should anticipate more reasonably priced OLED technology in a greater variety of gadgets as a result.
TCL recently declared its dedication to OLED display technology that is inkjet produced. Like MAX OLED, the business highlighted the production process’s scalability and cost-effectiveness, which may result in larger, more reasonably priced OLED screens. Compared to conventional techniques, TCL claims that their new inkjet-printed OLED has superior contrast, improved brightness control, and less production waste, making them appropriate for both consumer electronics and businesses.
With its new MAX OLED platform, Applied Materials has shown a revolutionary advancement in OLED display technology. High-quality displays will be possible on a wider variety of devices, such as PCs and TVs, thanks to this invention, which is expected to redefine the scalability and efficiency of OLED manufacturing.
It is said that switching from Gen 6 to Gen 8 glass substrates for OLED manufacture is the main breakthrough. Because Gen 8 substrates offer improved yield efficiency and optimize the number of displays produced per sheet of glass, this change enables manufacturers to make larger and more affordable OLED panels. The increasing need for bigger and more functional screens, particularly in consumer devices like laptops and tablets, is directly met by this scalability.
Additionally, MAX OLED technology promises notable enhancements in display performance. Compared to conventional OLED displays, panels made with this method are said to have a 5x longer lifespan, 2.5x higher resolution, and up to 3x brighter brightness. Furthermore, these improvements are made while using 30% less power, which makes the technology more ecologically friendly and energy-efficient.
The platform overcomes old obstacles in OLED manufacturing, like homogeneity and material waste, by integrating new materials and precision engineering techniques. The accuracy of material deposition is improved by its special co-evaporation technique, and production workflows are streamlined by proprietary tools. MAX OLED minimizes its impact on the environment and lowers expenses by optimizing material consumption.
The display business is changing as a result of the adoption of this new technology by top display manufacturers such as Visionox, Japan Display, and Samsung Display. Beyond high-end smartphones and TVs, OLED adoption may grow thanks to the capacity to mass produce affordable, high-quality OLED screens.
Customers should anticipate more reasonably priced OLED technology in a greater variety of gadgets as a result. TCL recently declared its dedication to OLED display technology that is inkjet produced. Like MAX OLED, the business highlighted the production process’s scalability and cost-effectiveness, which may result in larger, more reasonably priced OLED screens.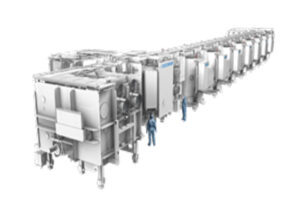
A Growing OLED Display Opportunity
With a wide range of devices covering CVD thin-film encapsulation, eBeam testing and inspection, and CVD** and PVD** deposition, Applied claims to be biggest supplier of display manufacturing equipment worldwide.
- Gen 6 glass panel surface area = 2.78 square meters; Gen 8 surface area = 5.5 square meters; Gen 10 surface area = 9.9 square meters
- PVD = physical vapor deposition; CVD = chemical vapor deposition.