One of the cornerstones of Industry 5.0 is its use of advanced technologies to create more holistic and effective manufacturing solutions. Naturally, sensors and data collection build the foundation for such an effort.
With data offering manufacturers unprecedented insights and transparency into their operations, Industry 5.0 unlocks new opportunities for efficiency, sustainability, and quality on the factory floor.
In this blog, we will look at the role of sensors and analytics in industrial automation and discuss how these technologies are central to Industry 5.0.
Developing Sensor Technology in Industrial Automation
Sensors have always been key to industrial automation. Early implementations focused on basic physical measurements, specifically pressure, temperature, level, and flow. But, as automation advanced, so did sensor technology.
In recent years, new categories of sensors—image, proximity, torque, vibration, and speed—have emerged to address the needs of more complex and diverse manufacturing environments.
In the context of Industry 5.0, manufacturing processes often involve human-robot collaboration, which necessitates additional safety measures. For example, proximity, image, and even infrared sensors have become essential to detect collisions in environments where humans work alongside collaborative robots (cobots).
These sensors protect operators by detecting motion in real time and triggering safety responses if a human enters a high-risk area.
Beyond safety, torque and displacement sensors assist robots in accurately positioning objects on conveyors to ensure operational accuracy and quality control. Such sensor diversity and adaptability make advanced industrial automation possible and support various manufacturing needs.
Optimizing Processes and Resources
In Industry 5.0, real-time data collection enables responsive and adaptable production environments. Here, sensors gather data on everything from conveyor speeds and object dimensions and shape to product completion rates and assembly quality.
For example, manufacturing operations on assembly lines use real-time sensor data to ensure that product components are correctly aligned and within tolerance, which prevents costly rework.
Real-time data are particularly important in applications where safety is a priority, such as automated assembly lines or hazardous manufacturing setups. In these scenarios, sensors provide instantaneous feedback to control systems, enabling preventive actions that protect personnel and maintain operational integrity.
By leveraging real-time sensor data, manufacturing systems can optimize the balance between productivity and safety, with minimal downtime from manual checks or disruptions. The role of generative AI (GenAI) has become increasingly pivotal to the significant increase in the computational power of modern smart factory control systems.
In a similar vein, sustainable productivity, one of Industry 5.0’s pillars, aims to reduce resource consumption and minimize waste while maximizing output. Sensors play a role in this effort by measuring energy consumption, production speed, material use, and enabling overall equipment effectiveness (OEE) calculations—a metric that indicates a machine’s effectiveness across factors like quality, performance, and availability.
With real-time data, manufacturing systems can quickly identify and address inefficiencies, such as machines running at suboptimal speeds and loads or producing excessive waste.
Advanced analytics platforms aggregate sensor data to calculate OEE. When a machine operates below target OEE levels, analytics can help identify specific inefficiencies, such as excessive idle time, poor energy use, and downtime, allowing managers to adjust for optimal performance.
For instance, analytics might suggest reducing the operation of a machine that consumes high energy or optimizing material use to minimize scrap. As a result, manufacturers achieve more sustainable operations while simultaneously improving profitability.
Enabling Predictive Maintenance
Predictive maintenance, which depends on long-term and real-time data collection from sensors, is one of the most valuable applications of analytics in industrial automation.
With years of historical data on equipment performance, analytics can predict maintenance needs before failures occur. While real-time data are crucial for immediate operational decisions, predictive maintenance relies on data trends gathered over months or even years.
For effective predictive maintenance, companies often integrate data from original equipment manufacturers (OEMs) with their own collected data. Given that OEMs have years of operational data from similar machinery, this collaborative approach allows access to a wider dataset.
For example, sensors installed in turbines or conveyor belts to monitor vibration, oil debris, temperature, or pressure, flag deviations that indicate wear or potential failure. Advanced analytics can then process these data and identify patterns that suggest when equipment likely will require servicing, thereby minimizing downtime and repair costs and extending the equipment’s operational life.
However, implementing predictive maintenance requires significant data volume and historical trend analysis. Thus, cloud computing becomes an integral part of the equation. By processing data at scale, cloud-based analytics platforms support high-precision maintenance scheduling and operational planning, directly optimizing productivity and cost efficiency.
Integrating Sensors in Legacy Systems
While Industry 5.0 emphasizes interconnected systems and data-driven processes, many industrial facilities still operate with legacy equipment designed for Industry 3.0 or 4.0 environments. Integrating modern sensors into these outdated systems presents unique challenges.
For example, legacy systems typically use analog sensors, which may not support the advanced data-processing capabilities required for Industry 5.0.
Retrofitting or adding sensors involves ensuring accurate placement, which may be difficult when access to certain machine components, such as rotating shafts or internal bearings, is restricted.
Furthermore, retrofitting requires infrastructure upgrades to accommodate digital communication, as analog wiring and interfaces often lack the bandwidth needed to handle real-time data transmission from multiple sensors. To bridge this gap, facilities may need to install data converters or even wireless communication systems to facilitate data transfer without overhauling the entire infrastructure.
Moreover, when integrating digital sensors, compatible software to analyze and visualize sensor data is needed, posing another challenge to legacy control systems. Therefore, companies moving toward Industry 5.0 must invest in sensor technology and supporting ecosystems, such as fiber optics, edge computing devices, and analytics platforms, that can manage and process data from these sensors.
Conclusion
As Industry 5.0 continues to evolve, sensors and analytics will only become more important. With their ability to monitor real-time conditions, predict maintenance needs, and support sustainability goals, sensors enable manufacturers to optimize processes while safeguarding workers and reducing environmental impact.
Meanwhile, advancements in analytics driven by GenAI will provide the intelligence necessary to make sense of the vast data these sensors generate. Together, these technologies are the foundation of Industry 5.0, turning data into actionable insights and paving the way for a more adaptive and resilient industrial future.
About the Author 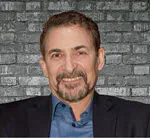
Hector Barresi is an award-winning Industrial Technology Advisor, Consultant, and Public Speaker specialized in Industrial Automation, Smart Manufacturing, and Digitalization. He has held executive positions at Honeywell, Danaher, IDEX and General Electric, and he is renowned for shaping top-tier Product Innovation organizations globally. Notably, he pioneered the Honeywell XYR5000, the first industrial wireless sensor family on the market, and the groundbreaking Tintelligence smart tinting platform, revolutionizing the paint industry.
The article was originally published on Mouser Electronics and has been posted on the Volt Post with approbation.