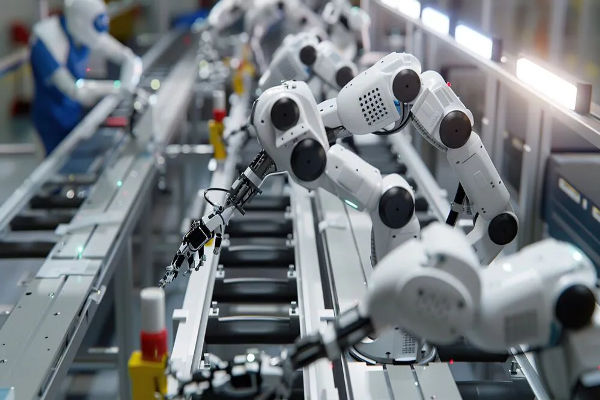
Without question, workplace injuries and illnesses significantly affect a company’s bottom line. In fact, according to a 2021 OSHA report,[1] estimates show companies pay almost US$1 billion per week for direct workers’ compensation costs.
Beyond these costs, company’s face indirect costs for workplace injuries and illnesses, including lost productivity that might result from training new employees or repairing damaged equipment.
When we discuss the benefits of Industry 5.0 in the modern factory, we must remember the most important element—the people. This new manufacturing era, with its advanced technologies, is not just about improved operational efficiency and productivity. It’s also about creating a safer and more efficient work environment, with the human worker at the center of it all.
In this blog, we’ll examine operational and functional safety in Industry 5.0 and how new technologies like collaborative robots (cobots) and drones, as well as an overall human-centric approach, are creating a safer environment for workers.
Operational vs. Functional Safety
As a whole, Industry 5.0 is unique in emphasizing a human-centric approach to safety. In the context of the modern factory, safety is defined as either operational or functional.
Functional safety involves designing and integrating safety systems that prevent accidents and system failures. These safety systems include establishing processes that mitigate potential faults and failures, incorporating equipment safety technologies, and creating safety designs that comply with industry regulations.
Wearable sensors are one example of Industry 5.0 safety systems. The wearable sensors monitor workers’ compliance with safety protocols, ensuring they wear the necessary protective gear and avoid restricted areas. Sensors embedded in gloves and helmets, for instance, can detect whether workers are wearing the required safety equipment and restrict access to hazardous areas if they are not.
Operational safety focuses on the day-to-day implementation and maintenance of these safety measures. It involves training personnel, maintaining equipment, and ensuring all safety protocols are followed during routine operations. In a manufacturing plant, operational safety includes ensuring workers follow safety guidelines and maintaining equipment properly to prevent accidents.
An example of operational safety in Industry 5.0 could be an artificial intelligence (AI)–based coaching system that can provide continuous feedback to workers on improving their safety practices. Such a system can analyze workers’ movements and suggest adjustments to their postures or actions to reduce the risk of injury.
New Technologies and Safety
Industry 5.0 is marked by the integration of new factory technologies, many of which are designed to enhance workplace safety.
Cobots, for instance, are meant to operate cohesively with humans, offloading intense and repetitive tasks from the worker.
Such a technology reduces the risk of musculoskeletal injuries and allows workers to focus on more complex and creative tasks. To achieve this, cobots are equipped with specialized force and proximity sensors that allow them to perceive and interact with their environment—including the humans—to better prevent collisions and reduce risks to human workers.
Similarly, a drone is another technology that improves safety in Industry 5.0. Drones are valuable in this context because they can reduce the need for human exposure to dangerous environments, including confined spaces, high elevations, or areas with toxic gases. Equipping drones with sensors, such as cameras, allows them to gather real-time data and quickly identify and resolve potential issues.
Finally, the exoskeleton is an Industry 5.0 innovation that assists workers in lifting heavy loads, thereby reducing the risk of injury. These wearable devices provide mechanical support, allowing workers to perform physically demanding tasks easily. Exoskeletons contribute to a healthier and safer workplace by minimizing the physical strain on workers.
The Role of AI and IoT
AI and the Internet of Things (IoT) fundamentally transform the concept of safety in the modern factory. Industry 5.0 leverages AI and advanced sensors to predict and prevent equipment failures.
These systems monitor parameters such as temperature, pressure, and vibration to detect potential issues before they lead to catastrophic events. Predictive maintenance uses sensor data to identify patterns and predict when maintenance is needed. Such a proactive approach minimizes downtime and enhances overall safety by addressing problems and potential accidents before they escalate.
Similar to a high-speed conduit, IoT connects all devices and systems within a plant, enabling real-time monitoring of all operational parameters and quick response to anomalies.
For instance, IoT-enabled sensors can monitor the environmental conditions within a plant continuously, such as humidity, temperature, and gas levels, and provide immediate alerts if any parameter deviates from safe limits. Instant feedback allows for swift corrective actions, minimizing the potential for developing hazardous situations.
With an interconnected approach, IoT allows for comprehensive safety management, which reduces the likelihood of accidents and improves overall operational efficiency. For example, if a sensor detects a temperature spike in equipment, the IoT system can shut down the equipment automatically and alert maintenance personnel.
Collectively, AI and IoT enable a holistic approach to safety management. With all safety systems and devices interconnected, environment, health, and safety (EHS) managers can access a centralized platform to monitor and manage safety protocols. A comprehensive view combined with the analytical capabilities of AI allow for better decision-making and more effective coordination of safety efforts across the entire plant.
Conclusion
Industry 5.0 transforms how we view operational and functional safety in the factory. By integrating advanced technologies, AI, and IoT, as well as focusing on human factors, Industry 5.0 creates safer, more efficient, and more productive manufacturing environments.
Sources
[1] https://www.osha.gov/businesscase/costs
About the Author
Hector Barresi is an award-winning Industrial Technology Advisor, Consultant, and Public Speaker specialized in Industrial Automation, Smart Manufacturing, and Digitalization. He has held executive positions at Honeywell, Danaher, IDEX and General Electric, and he is renowned for shaping top-tier Product Innovation organizations globally. Notably, he pioneered the Honeywell XYR5000, the first industrial wireless sensor family on the market, and the groundbreaking Tintelligence smart tinting platform, revolutionizing the paint industry.