The biggest producer of drive components in Taiwan, Hota Industrial has opted for the Mando G211 mandrel from Hainbuch and is currently being used by the Taichung-based company to produce electric car transmission parts.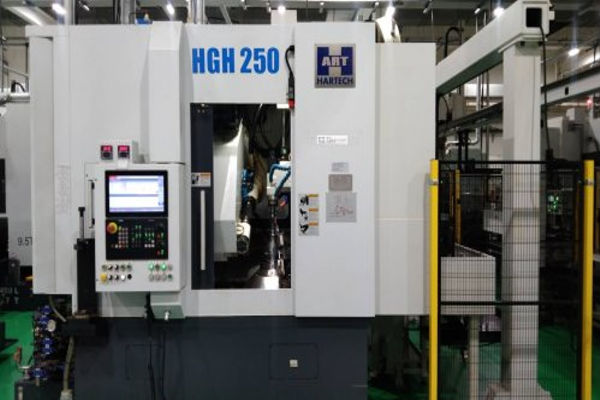
The low-alloy case-hardening steel that is utilized and the 20,000 units produced each month put a lot of strain on the equipment and machinery. Productivity increased by 20% as a result of the German workholding manufacturer meeting the standards.
In May 2021, Hota and Hainbuch started working together. To increase production quality and process reliability, the gear manufacturer intended to alter the clamping condition for every process step prior to hardening.
The Hartech HGH-250 gear hobbing machine is used to make the drive gears. The Hota Industrial Group’s mechanical engineering branch is called Hartech. In the past, Hota produced helical drive gears using collets. According to Alex Chao, Deputy Head of Design at Hota Industrial, “The collets did not meet the requirements for concentricity and repeatability for our production.”
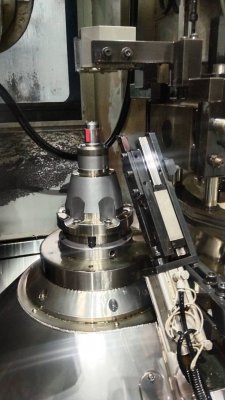
Convincing rigidity achieved
The chosen Mando G211 mandrel has a pull-back effect and clamps radially. The mandrel’s radial clamping force ranges from 42 to 150 kN, depending on its size. The necessary accuracy is provided by this incredibly rigorous I.D. clamping.
Chips are kept out of the clamping device by integrated flushing passages. The machining time per part is also decreased by the enhanced procedure. The mandrel’s segmented clamping bushings are vulcanized, which reduces vibrations while machining. Since the mandrel was placed, the tools’ service life has considerably enhanced.
20 percent less set-up time
The Mandrel Mando G211 has a longer service life than the collets that were previously in use. Chao explains the clamping device selection by saying, “The mandrel with the segmented clamping bushings offers high concentricity and also a long service life of the vulcanization.”
The G211’s narrow tool runout contour makes it perfect for gear manufacture, and it has also made managing the clamping devices easier for the operator. The mandrel’s maximum length is 213 mm.
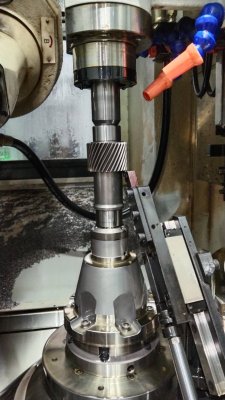
Additionally, a span range of 0.5 mm (clamping range 20-28 mm) to 0.9 mm (clamping range of the mandrel from 69-120 mm) is made possible by the vulcanized segmented clamping bushing. This facilitates workpiece diameter tolerance compensation during work preparation. The impact of altering to the mandrel from Hainbuch is a reduction in both set-up time and machining time by 20 percent.
Good service makes all the difference
The entire production process has been greatly enhanced by the choice of workholding technology. Alex Chao acknowledged that Hainbuch’s guidance had a significant role in his decision to choose the workholding manufacturer, saying, “We are very satisfied with the service and advice provided by the Hainbuch employees.” The stability, longevity, and favorable price-performance ratio of the Mando G211 mandrel made it stand out when compared to other manufacturers’ products. Hota intends to make the Hainbuch Mando G211 a standard feature for all upcoming machines.
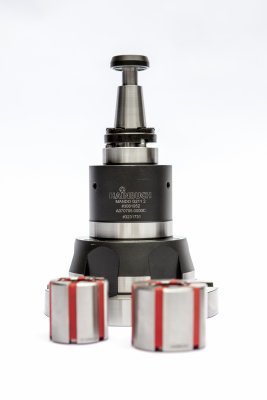
For Further Info, CLICK HERE