Inside the world’s mines, electrically powered equipment transports, crushes, and grinds rock, hauls raw materials, lights dark caverns, runs pumps and ventilation fans, and powers drills, cutting machines, dust collectors, and hoists.
Equipment failure leads to costly production downtime, so high reliability is expected despite vibration, impact, and exposure to chemicals, dust, heat, and moisture.
Designing electrical supply networks for this environment while ensuring worker safety is challenging but is helped by the availability of commercial electrical products certified to international operational and safety standards.
To simplify system design and ensure compatibility between components, designers can use a single source for much of the equipment needed to build a complete solution.
This article briefly outlines the environmental and power quality demands that mining places on electrical equipment. It then introduces examples of specialized solutions from SolaHD and explains how they can be applied in a multitiered approach to ensure power quality and worker safety.
The challenges of underground electrical engineering
In mines, equipment is subject to corrosive liquids, combustible dust, grime, harsh chemicals, heavy vibration, random impact, power surges, and extreme temperature variations. However, equipment and their power systems are expected to be safe and reliable.
Safety is bolstered by oversight from institutions such as the U.S. Mine Safety and Health Administration (MSHA) and the Federal Mine Safety and Health Act of 1977. Another U.S. standard is the National Electrical Code (NEC), or National Fire Protection Association (NFPA) 70.
This standard covers the safe installation of electrical wiring and equipment. NEC Article 500 requires installing code-compliant equipment tested and approved for specific hazards, including those found in mines and their surroundings.
Ensuring power quality requires understanding the basic power architecture and associated issues.
Mines generally draw their power from the AC grid, although high-voltage DC power, supplied by AC/DC conversion or onsite DC microgrids, is also used. Uninterruptible power supplies (UPSs) are an example. The systems follow a basic design: high-voltage power from the AC grid feeds high-voltage transformers that supply a main substation.
The main substation distributes energy to multiple secondary substations and directly to the mine’s larger motor loads. The secondary substations supply power to medium-voltage loads and medium/low-voltage transformers connected to other equipment.
While this supply grid is typically stable, power quality problems often arise. Such problems appear in the form of power interruptions, brownouts, voltage sags, voltage surges, voltage transients, harmonic distortions, and electrical noise (Figure 1).
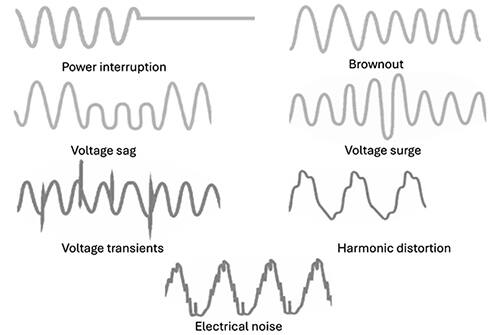
Consider the cause and effect of these power quality problems:
Power interruptions: These are complete power losses for an extended period, typically caused by an accident or equipment failure in the utility’s generation or distribution network. Power interruptions can cause hardware failures and crashes in computer-based equipment, halt operations, and decrease the lifespan of electrical equipment.
Brownouts: These describe what happens when the supplied voltage is below the normal minimum levels for an extended period. They occur when overcapacity or other network issues force utilities to lower the voltage to cope with the demand. The effects of brownouts are similar to those of interruptions.
Voltage sags: Sags and undervoltage conditions are the most common power quality disturbances in mining. They occur when a significant increase in load stresses the supply, causing the supply voltage to drop below a threshold level.
The IEEE defines a sag as a 10 to 90% voltage reduction below the normal 60 hertz (Hz) voltage. A sag event lasts less than one minute but more than 8 milliseconds (ms). Undervoltages last longer than a minute.
Both sags and undervoltages may cause nuisance breaker tripping, equipment malfunction and shutdown, or premature equipment failure. Continued operation elevates the risk of combustion or explosion.
Signs of these issues include dimmed or flickering lights, poorly operating HVAC units, motors running hot, and automation control systems and computers locking up or powering down.
Voltage surges: A surge or overvoltage condition is a temporary voltage level increase for a duration ranging from a half-frequency cycle to a few seconds. These disturbances can be caused by shutting down high-power electric motors and the normal cycling of HVAC systems. Repeated voltage surge exposure can stress and weaken systems and cause false trips of circuit breakers and other protection devices.
A further problem associated with overvoltages is insulation degradation. Deteriorating insulation jeopardizes the safe operation of the mine power system by serving as a catalyst for fires or triggering methane or coal dust explosions.
Voltage transients: Voltage transients, or spikes, result from sudden significant increases in voltage caused by external factors such as lightning strikes and utility grid switching. They can also originate inside the mine due to short circuits, tripped breakers, and heavy equipment starting up.
Sensitive electronic equipment is most at risk from voltage transients that can cause system lock-up or failure, corrupting or deleting valuable data.
Harmonic distortions: Voltage problems arise when multiples of the fundamental frequency (such as 180 Hz in a 60 Hz system) occur in the supply sinewave. Harmonic distortion exists due to the nonlinear characteristics of devices such as variable speed drives (VSDs) and loads on the power system.
The harmonics lead to increased heating in equipment and conductors, misfiring of VSDs, and torque pulsations in motors. Other symptoms of harmonic distortion in a mining power system are interference with the mine’s communication system, flickering lights, tripped breakers, and loosened electrical connections.
There are many electric motors in mines, most of which feature non-linear VSDs, making them the main source of harmonics in a mining operation. Moreover, using a full wave rectifier in the motors improves efficiency but generates considerable harmonics.
Electrical noise: This is a low amplitude, low current, and high-frequency disturbance generated inside and outside the mine. Sources include distant lightning strikes, switching power supplies, electronic circuits, poor motor-brush contacts, and poor-quality wiring.
The noise signals are superimposed on voltage waveforms and can cause computer glitches and undesirable effects in the circuits of control systems.
Addressing power quality problems
The best way to meet the critical challenges of continuous demand for high-quality power in mining, while ensuring robustness and high levels of electrical safety, is to adopt a multitiered approach using certified equipment that includes UPSs, power conditioners, surge protection devices (SPDs), transformers, and power supplies.
Table 1 summarizes the best equipment to control a particular power quality problem.
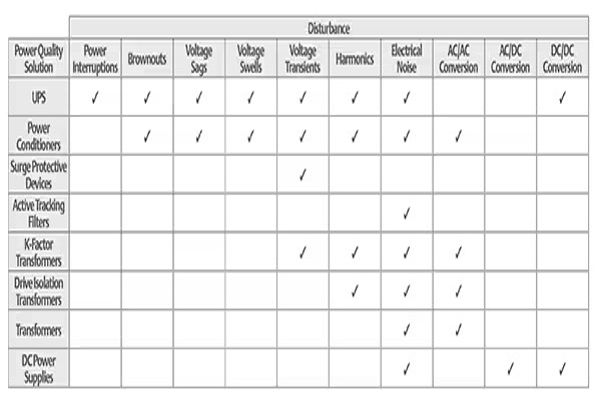
It is helpful to work with a single source, such as SolaHD, for a multitiered power quality approach to simplify the design, acquisition, and deployment process, as well as to ensure compatibility. For example, the company’s SDU500B offline UPS provides backup power for 4 minutes (min) and 20 seconds (s) at full load and 14 min and 30 s at half load in the event of a power interruption (Figure 2). As shown in Table 1, this UPS also supports the main power supply in the event of brownouts, voltage sags, voltage surges, voltage transients, and harmonics.
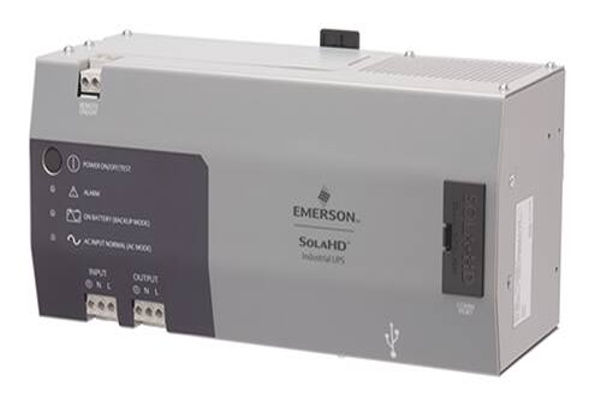
The UPS is DIN rail mounted and uses maintenance free, sealed lead-acid (SLA) batteries that are fully charged in eight hours. It provides a 300 watt, 120 volt output with a simulated sinewave of 50 to 60 Hz and a transfer time of less than 8 ms. The UPS can operate across a temperature range of 0 to 50?C and is a “Recognized Component” for Use in Zone Classified Hazardous Locations under E491259, making it suitable for mining operations.
SolaHD’s power conditioners can also regulate a voltage to within ±1% for input variations up to +10/-20%, provide superior noise attenuation, and are designed to withstand the harshest electrical environments.
The power conditioners use a transformer design technique called ferroresonance that creates two separate magnetic paths in the device with limited coupling. One advantage of this design is that the input current contains a negligible harmonic current relative to the fundamental. The output side of the transformer features a parallel resonant tank circuit and draws power from the primary to replace power delivered to the load.
The SolaHD 63-23-112-4 120 volt-ampere (VA) MCR Hardwire Regulator, for example, is a power conditioner that provides a 120 volt output (±3%) from a 120, 208, 240, or 480 volt input. It ensures excellent noise filtering and surge protection together with voltage regulation.
The noise attenuation is 120 decibels (dB) in common mode and 60 dB in transverse mode. Its surge protection is tested to ANSI/IEEE C62.41 Class A & B Waveform. The MCR Hardwire Regulator is a good choice when brownouts, voltage sags, surges, transients, harmonics, and electrical noise are expected.
SPDs protect against equipment-damaging voltage transients. SolaHD’s STV25K-24S transient voltage surge suppressor (TVSS) SPD is a DIN rail mount device that operates from a 240 volt input (up to 20 A) and provides point-of-use protection by using a metal oxide varistor (MOV) (Figure 3).
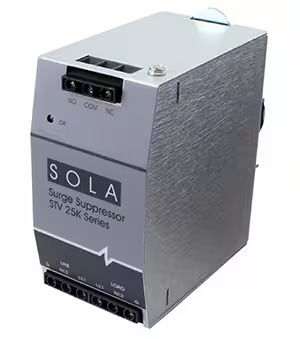
The SolaHD SPD is suitable for installation in control cabinets in harsh industrial environments such as a mining facility. The device provides 25,000 A of surge protection per phase. The response time to a transient is less than 5 nanoseconds (ns). The SPD incorporates thermal fusing to prevent MOV overheating caused by excessive current levels.
Specifying isolation transformers and power supplies
In addition to stepping up or down an input AC voltage to a suitable output value, isolation transformers can protect devices connected to the secondary side from harmonics and electrical noise.
One example is the SolaHD E2H112S. This isolation transformer is an energy-efficient dry type that features a weather shield. It has a 480 volt primary input (up to 135 A), offers 208 or 120 volts from the secondary (up to 315 A), and is rated at 112.5 kilovolt-amperes (kVA) (Figure 4). The transformer also mitigates harmonics and electrical noise.
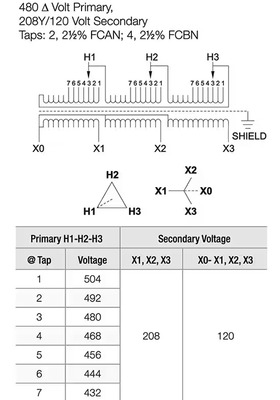
The transformer should be protected against inrush currents by a circuit breaker. It is good design practice to select a circuit breaker device with a suitable time delay to eliminate nuisance tripping. This phenomenon occurs when the inrush current is high but is of insufficient duration to damage the transformer.
Power supplies are vital to any electrical supply system, providing AC or DC power to equipment and helping filter out electrical noise from the main supply. DIN rail mount versions are tidy and save space. Single and three-phase AC models are available; it is also possible to specify devices capable of handling voltage sags down to half the line voltage with no disruption in output power.
SolaHD provides a range of DIN rail power supplies, such as the SDN5-24-100C AC/DC supply (Figure 5). This is a single-phase supply and complies with the Hazardous Location E234790 specification. It can accept an 85 to 264 volt AC (VAC) input or a 90 to 375 volt DC (VDC) input, supplying a nominal 24 volt output.
The output current is 5 A. The voltage ripple on the output is less than 50 millivolts (mV) peak-to-peak. The power supply features high electromagnetic interference (EMI) immunity and an operating temperature range of -25 to +60?C. It is compact, measuring 123 x 50 x 111 mm, and protected against continuous short circuit, continuous overload, and continuous open circuit faults.
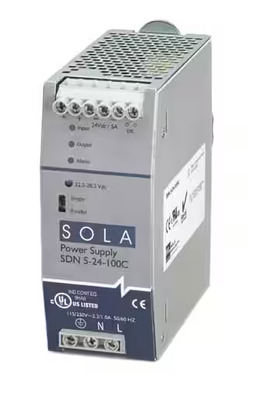
Article Source: www.digikey.in