New options are available for the R&S AREG800A automotive radar target simulator from Rohde & Schwarz. An environment for a seamless transition of automotive radar sensors from R&D to production is created and made possible by the new R&S AREG-P. By utilizing the AREG-P either independently or as a turnkey solution in conjunction with NOFFZ’s integration into their production test systems, Tier 1 automotive radar suppliers can enhance their throughput, minimize test duration, and optimize end-of-line test expenses.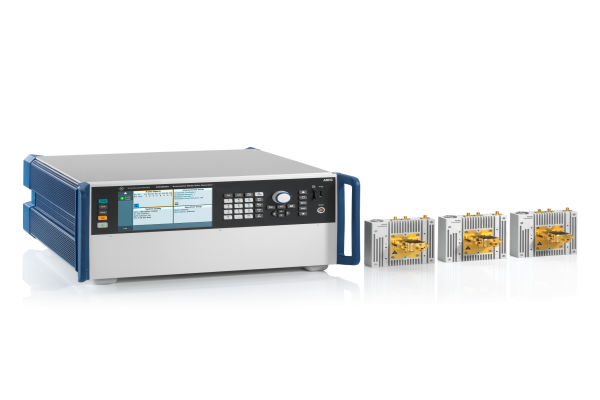
A seamless transition is essential when producing radar sensors from R&D. The production models will fulfill the same exacting performance, reliability, and durability standards that were set during the research and development stage if the changeover is handled smoothly. Any issue during the transition could jeopardize these features and put drivers and other road users at risk.
The Well-Known AREG800A Radar Target Simulator
A world-renowned radar target simulator, the AREG800A, is the foundation for the R&S AREG-P, which is made to successfully handle these test and measurement challenges with its highly versatile configuration and precise parameters.
Its modular design provides adaptation to various production needs. It consists of a base unit, up to three fully digital channels for independent generation of artificial objects and one object per channel, and the possibility to link up to three frontends to a single base unit.
The radar under tests EIRP can be measured using an additional R&S NRP8S(N) diode power sensor and bandwidth using an additional R&S FSV3007 signal and spectrum analyzer thanks to a broad 5 GHz RF instantaneous bandwidth and analog IF output interfaces. This not only promotes quality assurance and regulatory compliance but also guarantees that production models live up to the high performance criteria set during the R&D phase.
A range of models are available from the R&S AREG-P, each specifically designed to address various requirements and operational contexts in radar production applications.
The Radar Mini configuration, represented by R&S AREG-P1, enables a smooth transition of the top radar test technology in the world into the radar production application. The Radar Golden configuration of R&S AREG-P2 enables the simultaneous, parallel testing of two radars in separate chambers during manufacturing while utilizing the same target simulator.
Save Testing Time in Production
To save testing time in production, the Radar Pro configuration R&S AREG-P3 takes one step further by doing away with the requirement for azimuth sweeps. The most sophisticated option is provided by the R&S AREG-P2+3, also known as the Radar Golden-Pro configuration, which further minimizes production testing time by doing away with both the azimuth and elevation sweeps.
For automotive radar production testing, the new choices are future-proof and optimized by utilizing the strength of the R&S AREG800A. Furthermore, the production phase can now benefit from the established AREG target simulator’s proven performance thanks to the AREG-P technology.
In addition to the AREG-P, the CATR reflector technology has also been put into production, providing still another technological advantage by allowing automobile radar sensor tests to be conducted in remote fields with a small test stand footprint. CATR is future-proofed for expanding antenna apertures and has already demonstrated its efficacy in testing cutting-edge 4D radars.
Lastly, customers building radars in the R&S ATS1500C chamber with the R&S AREG800A have a seamless yet small production testing option with the AREG-P and the CATR reflector.
R&S AREG-P Solutions Benefits
Significant business benefits are also provided by the R&S AREG-P solutions, which can improve operational effectiveness and profitability in the manufacture of automotive radars. Its modular design facilitates the distribution and minimization of capital expenditures (CAPEX). Because of its excellent performance accuracy, it reduces Time to Market (TTM) and Operational Expenditure (OPEX).
The small footprint of the design reduces CO2 emissions and creates testing locations that are favorable to the environment. The R&S AREG-P systems’ scalability and flexibility, together with its quick and simple deployment that cuts down on setup time and related expenses, all help to save OPEX.
When automobile radar sensors are smoothly transferred from R&D test systems to production testing, failure risk is decreased and First Pass Yield (FPY) is raised, which lowers waste and boosts productivity.
Important features like variable object distance are moved from research and development to production, along with patents like airgap—a minimum distance for FMCW radar sensors and vertical chambers with CATR.
Ludwig Mair, Business Development Manager Radar from NOFFZ Technologies, comments: “At NOFFZ, we’re happy to work hand-in-hand with Rohde & Schwarz to integrate the R&S AREG-P into our test systems for end-of-line production. This collaboration enables us to offer our customers an unparalleled advantage in terms of performance, cost-efficiency, and environmental sustainability.”
In conclusion, every R&S AREG-P model has a distinct set of advantages and can provide a variety of solutions to satisfy the various demands of the dynamic and rigorous automotive radar production industry.
For Further info: CLICK HERE