The Growing Importance of Analog ICs
Despite the rapid growth of digital technology, analog integrated circuits (ICs) continue to play a crucial role in modern electronics. Analog ICs handle continuous signals such as temperature, sound, light, and pressure—making them essential for AI, IoT devices, autonomous vehicles, and power management systems.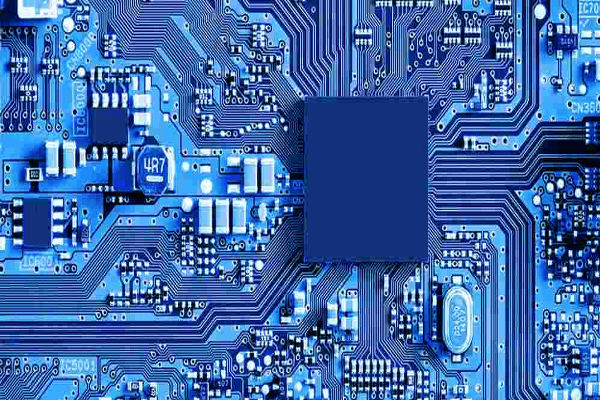
The global analog IC market is projected to reach $91.89 billion in 2025, with a 7.1% compound annual growth rate (CAGR). This surge is driven by increasing demand for compact, energy-efficient, and high-performance semiconductor solutions.
Recognizing this opportunity, two Japanese companies—Oki Electric Industry Co. (OKI) and Nisshinbo Micro Devices—have pioneered a breakthrough in thin-film 3D analog IC technology. Their new approach enables stacked analog ICs, reducing costs, size, and energy consumption while enhancing performance.
Advancements in Thin-Film 3D Analog ICs
The OKI-Nisshinbo Collaboration: Innovation Through Stacking
In January 2025, OKI and Nisshinbo announced their successful development of stacked thin-film analog ICs using an advanced fabrication process called Crystal Film Bonding (CFB).
How Does the CFB Process Work?
-
Lifting Off the Thin-Film Layer
- The functional layer of the analog IC is detached from the substrate using the CFB process (details remain a trade secret).
-
Stacking the IC Layers
- The thin-film layer is then bonded onto another analog thin-film layer using intermolecular bonding (which relies on molecular attraction rather than adhesives).
- The layers are insulated with materials like silicon oxide to prevent electrical interference.
-
Connecting the Stacked Layers
- Unlike traditional stacking techniques that use Through-Silicon Via (TSV)—a complex and costly vertical wiring method—CFB allows for more cost-efficient electrical connections using conventional semiconductor lithography.
Advantages Over Traditional Stacking Methods
Feature | CFB Stacking | Traditional TSV Stacking |
---|---|---|
Chip Thickness | 5-10 µm | Tens to Hundreds of µm |
Manufacturing Cost | Lower (uses existing lithography) | Higher (requires advanced equipment) |
Complexity | Simpler bonding process | Requires specialized TSV processing |
Scalability | Supports up to 4-layer stacking | Limited by TSV constraints |
Expert Insights on the Breakthrough
Kenichi Tanigawa, General Manager of OKI’s CFB Development Department, emphasizes:
“Our CFB stacking process allows for thinner chips and easier integration without the expensive TSV process. This means we can scale up production more cost-effectively while maintaining high performance.”
Toshihiro Ogata, Assistant Manager at Nisshinbo, explains the importance of analog ICs:
“We live in an analog world of sound, light, temperature, and pressure. Analog ICs act as the bridge between the physical and digital worlds, processing real-world signals into digital data.”
Addressing Cross-Talk and Signal Interference
One major challenge with stacking ultra-thin analog ICs is cross-talk—when signals interfere between stacked layers, causing noise and performance degradation.
Nisshinbo’s Proprietary Shielding Solution
To combat this, Nisshinbo developed a unique aluminum-based shielding technology:
- Localized Shielding: Instead of shielding the entire circuit (which increases unwanted capacitance), Nisshinbo only shields critical areas to prevent interference.
- High Voltage Compatibility: Unlike digital ICs that operate below 5V, analog ICs handle up to 30V—which increases the risk of signal degradation. Nisshinbo’s method reduces this risk while preserving circuit functionality.
Ogata from Nisshinbo highlights:
“Applying shielding only to the necessary areas allows us to reduce interference without negatively affecting the circuit’s performance.”
The Role of Thin-Film Analog ICs in Chiplet Integration
The shift toward chiplet-based architectures in semiconductor manufacturing is gaining momentum. Chiplets are modular ICs that can be combined to form a single, more powerful chip.
Benefits of Using Thin-Film 3D Analog ICs in Chiplets
Optimized Performance – Each chiplet can be customized for sensing, processing, or power management, enhancing overall system efficiency.
Reduced Size – Stacking ICs results in smaller and thinner devices.
Higher Yield – Defective chiplets can be replaced before full assembly, improving manufacturing success rates.
Gordon Roberts, Professor of Electrical Engineering at McGill University, sees this as a crucial step:
“The chiplet approach is vital for next-generation semiconductors. If OKI and Nisshinbo can integrate thin-film analog ICs with chiplets, we’ll see new levels of performance in AI, IoT, and mobile devices.”
Market Outlook: The Future of Analog ICs
The global analog IC market is booming, with demand surging across industries:
- AI & IoT – Edge computing requires low-power analog ICs for real-time data processing.
- Automotive – EVs and autonomous vehicles rely on analog ICs for power regulation, lidar, and sensor integration.
- 5G & Telecom – Next-gen networks need high-speed analog signal processing.
Projected Growth Trends
- 2024 Market Value: $85.78 billion
- 2025 Market Projection: $91.89 billion
- CAGR (2024-2028): 7.1%
Tanigawa from OKI confirms their long-term vision:
“We are preparing for mass production of thin-film 3D analog ICs by 2026, with applications ranging from chiplets to AI-driven electronics.”
The Future of Thin-Film 3D Analog ICs
The collaboration between OKI and Nisshinbo represents a significant milestone in semiconductor technology. Their thin-film 3D analog ICs offer a cost-effective, scalable, and high-performance alternative to traditional stacking methods.
Key Takeaways:
- CFB stacking simplifies 3D integration with thinner and more efficient ICs.
- Shielding technology minimizes cross-talk and interference.
- Chiplet integration opens new opportunities for AI, IoT, and automotive applications.
- Market growth suggests strong demand through 2028.