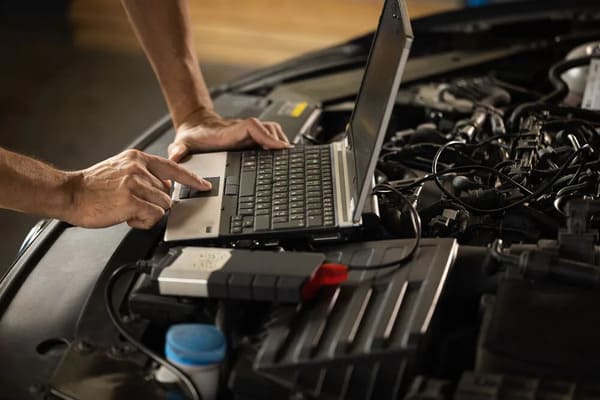
Regardless of their motive power source, today’s cars are packed with “electronics.” The electronics-related content in cars is substantial and continues to grow each year. This includes powertrains, advanced driver assistance systems (ADAS), comfort, entertainment, convenience, navigation, safety, and more.
Additionally, there is a less visible but equally important electromechanical component in cars: electric motors. Pure electric and hybrid electric vehicles (EVs and HEVs) have traction motors for propulsion, unlike cars with an internal combustion engine (ICE). However, all types of vehicles now incorporate numerous electric motors for various functions.
How many electric motors are there in a car? The answer varies. A medium-class car typically has around 40 electric motors (excluding traction motors), while premium-class vehicles can have up to double that number.
Electric motors are used for water and fuel pumps, adaptive suspension controls, blowers, compressors, power steering, windshield wipers, window lifts, and more (Figure 1). The specifics vary not only with the car’s luxury level but also with the type of powertrain; for example, the fuel pump is not needed in an electric vehicle.
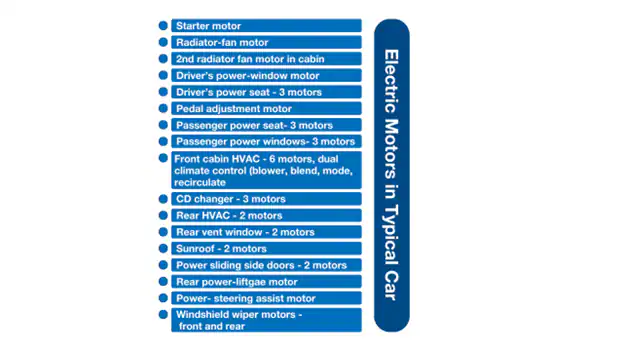
Obviously, the type, size, speed/torque, and motor operation for each of these motors are optimized by the location and application. These are divided into three major categories (Figure 2):
- Performance-related motors
- Comfort-related motors
- Volume motors
Figure 2: Electric motor applications can be categorized into three general groups, reflecting the importance of the associated function and the distinctiveness of the motor type. (Source: Author)
No single type of motor can meet every need, even if its size is scaled to the mechanical output power requirements.
Besides the various traction motors in EVs and HEVs, cars utilize a mix of motor types, including brushed DC motors, brushless DC motors (BLDC), and induction motors. The choice depends on factors such as load type, duty cycle, available space, and other considerations.
The Past Does Not Always Point to the Present
The first gasoline-powered cars that emerged around 1900 had neither motors nor batteries. They were started by hand-cranking and used a magneto—a simple, low-efficiency electrical generator with permanent magnets and a moving coil—to produce periodic pulses of alternating current for the spark-producing circuit.
The first motor in a car was the electric starter, introduced by Cadillac in 1912 and quickly adopted by nearly all cars. It relied on a basic 6V battery and remained the sole electric motor in cars for many years.
Later, features like in-car AM radio in the 1930s and power windows in the 1950s and 1960s necessitated an increase in battery voltage to 12V, but the number of motors remained in the single digits.
Many functions, such as the air conditioner compressor and power steering assist, were driven by a power take-off belt attached to the engine shaft, while others used air pressure or vacuum derived from the car’s engine.
These motors were connected and directed to the battery subsystem with point-to-point wiring, each controlled by an on-off switch. As the number of motors and their loads increased, the amount of wiring and the space and weight required became a design challenge and unsustainable burden.
In contrast, none of the motors in today’s cars are connected in this simple, direct, yet ultimately burdensome way. Instead, each has a motion- and motor-control IC and a solid-state power switch.
This switch is usually a silicon MOSFET integrated into the control IC for smaller motors or a separate discrete device for larger ones.
Depending on the function of the motor, a position-feedback sensor may also be used to provide motion management, ranging from a basic control-and-driver arrangement to a sophisticated, processor-controlled function.
The Power Window: An Illustrative Example
In just a few decades, we’ve progressed significantly from the days of manually operated car windows, outside mirrors, and door locks.
Today, these features are all electrically powered with no manual backup. Designing and delivering controlled power for the various motors and mechanisms in modern, complex door systems—and their adjuncts—is a substantial engineering challenge.
By examining car windows, we see the evolution of electric motors in vehicles. Fifty years ago, all car windows were operated manually using a mechanical linkage and a simple hand-powered rotary crank, known to designers as the “window winder.”
Each occupant had to manage their own window using their arm as the power source (Figure 3), while the car’s driver could only open or close the adjacent window instead of all four windows.
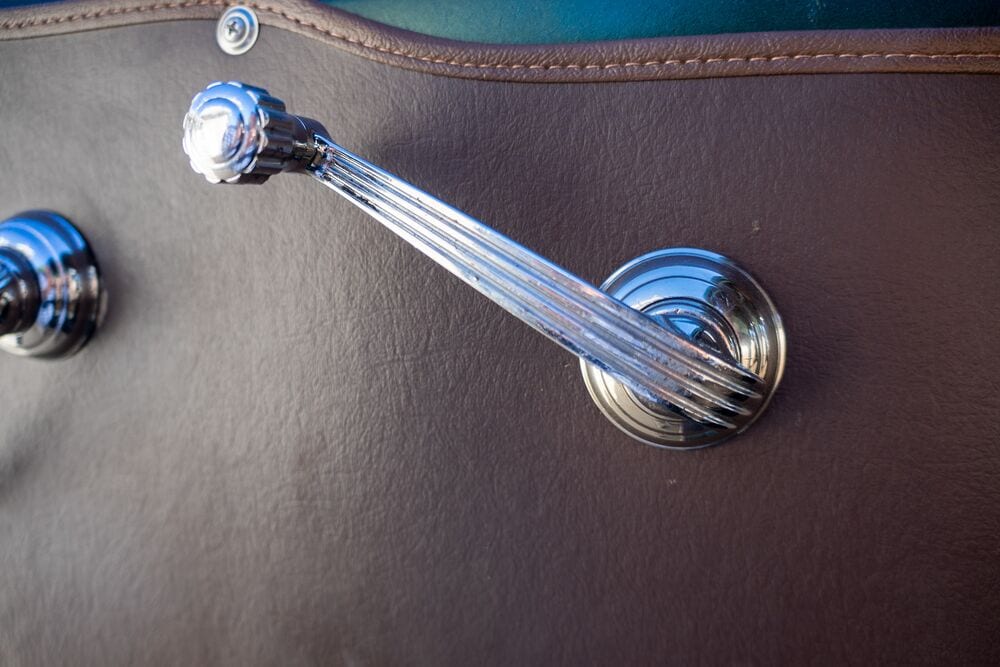
If your window winder broke, you could easily get a replacement at any auto supply store. Decorative aftermarket cranks were also popular.
Power windows were first introduced in the 1940s, initially using an electrically controlled hydraulic system to drive the window regulator, which is the mechanism that controls the movement of the window. These hydraulic systems were necessary because small electric motor technology was not yet advanced enough to be used inside the doors.
Then, in the 1960s, Cadillac Fleetwood models came standard with windows powered entirely by electric motors.
Within about a decade, power windows became a common feature in most cars, marking a swift adoption rate. By the early 21st century, car doors had evolved into complex electromechanical systems with all functions controlled electronically, eliminating the need for mechanical backups.
There was a transitional period when both electrical and mechanical controls were used to address customer concerns and provide reassurance.
For a while, two basic mechanism types were used for the window regulator: the cable type and the gear-drive type.[1] Regardless of the mechanical design used, both systems shared a common electrical aspect.
Unregulated 12V DC power flowed directly from the car battery to the motor via individual control switches for each window. Consequently, adding this “convenience feature” to the car increased the burden of thicker cable harnesses and the challenges of routing them throughout the vehicle.
Fortunately, the migration to low-speed networks such as the Controller Area Network (CAN bus), Local Interconnect Network (LIN Bus), or others within the car has reduced the cable-harness dilemma.
Now, unswitched 12V power goes to a regulator-motor controller in the door. At the same time, a networked switch with thinner cabling can communicate with the motor controller to control the window’s movement and monitor its performance.
However, what started as a basic network-friendly window motor controller soon evolved into a smart, processor-based controller with advanced performance capabilities.
The enhanced window network interface and motor controller IC require more sophisticated power management and regulation, and that’s where a power management IC (PMIC) is needed.
This sophisticated motor-related IC must be monitored and managed. The PMIC needs to include a self-test to promptly detect any excessive variations of power or other problems and take appropriate action immediately before there is any damage to the motor or associated components.
Application-specific window motor ICs and PMICs integrate these necessary functions into a single, smart IC.
Conclusion
The widespread adoption of affordable, high-performance electric motors in cars, each tailored to and controlled for a highly localized function, represents a significant advance in materials, motor design, electronics, and production.
Today, we take for granted the presence of features like power windows, now a standard in the modern automobile.
While electric motors were once large, heavy, inefficient, and difficult to control, they have now become compact models of efficiency. This advancement allows designers to use them without concern for practicality, easily solving design problems or adding new car features.
About the Author
Bill Schweber is a contributing writer for Mouser Electronics and an electronics engineer who has written three textbooks on electronic communications systems, as well as hundreds of technical articles, opinion columns, and product features. In past roles, he worked as a technical web-site manager for multiple topic-specific sites for EE Times, as well as both the Executive Editor and Analog Editor at EDN.
At Analog Devices, Inc. (a leading vendor of analog and mixed-signal ICs), Bill was in marketing communications (public relations); as a result, he has been on both sides of the technical PR function, presenting company products, stories, and messages to the media and also as the recipient of these.
Prior to the MarCom role at Analog, Bill was associate editor of their respected technical journal, and also worked in their product marketing and applications engineering groups. Before those roles, Bill was at Instron Corp., doing hands-on analog- and power-circuit design and systems integration for materials-testing machine controls.
He has an MSEE (Univ. of Mass) and BSEE (Columbia Univ.), is a Registered Professional Engineer, and holds an Advanced Class amateur radio license. Bill has also planned, written, and presented on-line courses on a variety of engineering topics, including MOSFET basics, ADC selection, and driving LEDs.
You must be logged in to post a comment.